Mitsubishi Motors Corporation (MMC) and its distributor in Singapore Cycle & Carriage Automotive PTE Limited (CCA) today announced the signing of a Cooperation Agreement to collaborate on activities to popularize electric vehicles (EV) with the Singapore government.
The Economic Development Board (EDB) of Singapore, including Singapore's Energy Market Authority (EMA) and Land Transport Authority (LTA), as part of a multi government agency EV task force will set up an EV charging infrastructure network and evaluate the cost benefits of EVs for future adoption. Within these activities, MMC, via CCA, will supply 25 i-MiEVs from 2011 and cooperate in the taskforce's test bedding efforts.
Mr. Leo Yip, Chairman, Singapore Economic Development Board said, "We are delighted to welcome Mitsubishi Motors on board as the first major EV supplier for Singapore's EV test bed programme. This test bed programme is an excellent example of how Singapore presents itself as a Living Laboratory for auto-manufacturers, charging equipment suppliers and EV component players to explore R&D and capability development activities in Singapore. We see opportunities in areas such as battery management systems, power electronics and electric drive systems. Companies can leverage Singapore's electronics cluster and engineering talent to build new capabilities here."
Mr. Osamu Masuko, President of Mitsubishi Motors said, "MMC is proud to be the part of EV test-bed in Singapore. We believe that Singapore is an ideal market for EV. Working together with the Singapore government and Cycle & Carriage Automotive, we would like to evaluate the performance of i-MiEV under the condition in Singapore and also promote the appeal of EV toSingapore citizen."
MMC is currently selling the i-MiEV in Japan, Hong Kong, and Australia. In addition, MMC has engaged in initiatives to popularize EVs with various governments all over the world, including the governments of the Principality of Monaco, Iceland, Denmark, among others.
Nov 28, 2010
GM Inaugurates Flexi-Engine Plant in Talegaon, India
General Motors today inaugurated its new flexi-engine facility in Talegaon, GM's first powertrain plant that enables petroleum and diesel engines to be manufactured simultaneously.
The state-of-the-art facility represents investment of $230 million. It has an initial annual production capacity of 160,000 engines and is designed to accommodate future expansion. The new engine plant will begin by producing engines for small passenger cars manufactured by GM in India.
"This marks the beginning of GM's next chapter in India." GM India President and Managing Director Karl Slym said. "The opening of our new facility will enable our company to become more competitive and keep up with the growing demand for our vehicles. GM India's sales have grown significantly since we began rolling out our mini-cars, the Chevrolet Spark and Beat, at our Talegaon plant about two years back."
Slym added, "We appreciate the support of the Maharashtra government and our employees across the country. Their backing has enabled us to build a world-class engine facility in record time of less than two years."
On Aug. 28, 2008, GM signed an agreement with the Government of Maharashtra for the construction of a new engine plant adjacent to its vehicle manufacturing facility. Construction started in December 2008, with pilot production commencing in March 2010. The engine plant complements GM's modern vehicle manufacturing facilities in Talegaon and Halol, Gujarat, as well as the GM Technical Centre – India in Bangalore, which is carrying out a range of engineering, design and R&D activities.
General Motors India has completed 14 years of operation. It offers a growing range of products under the Chevrolet brand, which was introduced in India in 2003 and has become one of the fastest-growing automotive nameplates in the country. In addition to the Spark and Beat, GM India also produces the Captiva, Optra, Cruze, Aveo, Aveo U-VA, and Tavera for sale nationwide.
GM is the fifth-largest automobile manufacturer in India. In the first 10 months of 2010, GM India sold a record 93,960 vehicles, which represents a 73 percent increase over the same period last year. It has 209 sales points and 205 service outlets in 178 cities across India, and has embarked upon an ambitious rural marketing initiative to further boost sales. In February 2010, GM and its Chinese partner SAIC opened a joint venture in India for cooperation in vehicle manufacturing and sales.
The state-of-the-art facility represents investment of $230 million. It has an initial annual production capacity of 160,000 engines and is designed to accommodate future expansion. The new engine plant will begin by producing engines for small passenger cars manufactured by GM in India.

"This marks the beginning of GM's next chapter in India." GM India President and Managing Director Karl Slym said. "The opening of our new facility will enable our company to become more competitive and keep up with the growing demand for our vehicles. GM India's sales have grown significantly since we began rolling out our mini-cars, the Chevrolet Spark and Beat, at our Talegaon plant about two years back."
Slym added, "We appreciate the support of the Maharashtra government and our employees across the country. Their backing has enabled us to build a world-class engine facility in record time of less than two years."
On Aug. 28, 2008, GM signed an agreement with the Government of Maharashtra for the construction of a new engine plant adjacent to its vehicle manufacturing facility. Construction started in December 2008, with pilot production commencing in March 2010. The engine plant complements GM's modern vehicle manufacturing facilities in Talegaon and Halol, Gujarat, as well as the GM Technical Centre – India in Bangalore, which is carrying out a range of engineering, design and R&D activities.
General Motors India has completed 14 years of operation. It offers a growing range of products under the Chevrolet brand, which was introduced in India in 2003 and has become one of the fastest-growing automotive nameplates in the country. In addition to the Spark and Beat, GM India also produces the Captiva, Optra, Cruze, Aveo, Aveo U-VA, and Tavera for sale nationwide.
GM is the fifth-largest automobile manufacturer in India. In the first 10 months of 2010, GM India sold a record 93,960 vehicles, which represents a 73 percent increase over the same period last year. It has 209 sales points and 205 service outlets in 178 cities across India, and has embarked upon an ambitious rural marketing initiative to further boost sales. In February 2010, GM and its Chinese partner SAIC opened a joint venture in India for cooperation in vehicle manufacturing and sales.
Nov 1, 2010
CANADA POST BECOMES FIRST CUSTOMER FOR AZURE DYNAMICS AND FORD OF CANADA'S TRANSIT CONNECT ELECTRIC VAN
Azure Dynamics Corporation (TSX: AZD)(OTC: AZDDF) ("Azure" or the "Company"), the fast growing hybrid electric and electric power train innovator for the commercial truck market, and Ford Motor Company of Canada, Limited, announced today that they will deliver one of the first Transit Connect Electric commercial vans to Canada Post under the LEAD customer program. Canada Post will receive one of the exclusive Ford Transit Connect Electric delivery vehicles by the end of this year and has committed to the purchase of nine more by end of 2011.
"Canada Post is the first Canadian company to sign on to this exclusive and innovative vehicle program aimed at providing environmental solutions to the commercial delivery market," said Scott Harrison, Azure Dynamics CEO. "The transformative technology of the Transit Connect Electric reduces gasoline fuel costs to zero, produces no tailpipe emissions and is virtually silent as it travels through urban and suburban delivery routes. The progressive attitude of companies like Canada Post will contribute to making an important environmental impact."
The new van's electric drive performance attributes are well suited to fleets like Canada Post that have duty cycles characterized by predictable routes with frequent stop and go driving and high idle time.
"As one of the largest communications and logistics companies in Canada, we're proud to be among the first to implement a fully electric delivery vehicle on our roads," says Doug Jones, Senior Vice President, Operations at Canada Post. "We expect that this new vehicle will bring us one step further along our path to reduce both our overall fuel emissions and our carbon footprint on the environment."
The Transit Connect Electric integrates Azure's Force Drive™ electric powertrain into Ford's dedicated global commercial van platform that received the 2010 North American Truck of the Year award. Its unique combination of car-like driving dynamics, cargo capacity, maneuverability, accessibility and low operating costs are characteristics that make the Transit Connect an ideal choice for electrification.
"At Ford, we are dedicated to delivering quality, safe and fuel efficient vehicles to Canadian businesses – and the Ford Transit Connect delivers on all fronts," said David Mondragon, president and CEO, Ford of Canada. "The Ford Transit Connect Electric represents a win-win for both the environment and for Canada Post – it allows them to operate a more environmentally-friendly vehicle while helping to reduce their CO2 emissions as well as their need for gasoline."
The Ford Transit Connect Electric utilizes an advanced lithium-ion battery from Johnson Controls-Saft to achieve a range of up to 130 km (80 miles) on a single charge and is rechargeable using either a 240-volt or standard 120-volt outlet. Commercial vans generally return to a central location at the end of each driving cycle making for easy overnight recharging.
"Canada Post is the first Canadian company to sign on to this exclusive and innovative vehicle program aimed at providing environmental solutions to the commercial delivery market," said Scott Harrison, Azure Dynamics CEO. "The transformative technology of the Transit Connect Electric reduces gasoline fuel costs to zero, produces no tailpipe emissions and is virtually silent as it travels through urban and suburban delivery routes. The progressive attitude of companies like Canada Post will contribute to making an important environmental impact."
The new van's electric drive performance attributes are well suited to fleets like Canada Post that have duty cycles characterized by predictable routes with frequent stop and go driving and high idle time.
"As one of the largest communications and logistics companies in Canada, we're proud to be among the first to implement a fully electric delivery vehicle on our roads," says Doug Jones, Senior Vice President, Operations at Canada Post. "We expect that this new vehicle will bring us one step further along our path to reduce both our overall fuel emissions and our carbon footprint on the environment."
The Transit Connect Electric integrates Azure's Force Drive™ electric powertrain into Ford's dedicated global commercial van platform that received the 2010 North American Truck of the Year award. Its unique combination of car-like driving dynamics, cargo capacity, maneuverability, accessibility and low operating costs are characteristics that make the Transit Connect an ideal choice for electrification.
"At Ford, we are dedicated to delivering quality, safe and fuel efficient vehicles to Canadian businesses – and the Ford Transit Connect delivers on all fronts," said David Mondragon, president and CEO, Ford of Canada. "The Ford Transit Connect Electric represents a win-win for both the environment and for Canada Post – it allows them to operate a more environmentally-friendly vehicle while helping to reduce their CO2 emissions as well as their need for gasoline."
The Ford Transit Connect Electric utilizes an advanced lithium-ion battery from Johnson Controls-Saft to achieve a range of up to 130 km (80 miles) on a single charge and is rechargeable using either a 240-volt or standard 120-volt outlet. Commercial vans generally return to a central location at the end of each driving cycle making for easy overnight recharging.
Oct 29, 2010
Kia introduces new Soul Flex at Brazilian Motor Show
(SEOUL) October 27, 2010 – Kia Motors is celebrating the world premiere of its new fuel efficient, ethanol-gasoline powered Soul Flex today (Wednesday), at the 26th Salao Internacional do Automovel, in S?o Paulo, Brazil.
Kia's Soul Flex is the first Korean FFV (Flexible Fuel Vehicle) which can run on an ethanol-gasoline mixture, 100% ethanol or 100% gasoline. It is especially designed for the Brazilian market, where 'flex' models account for more than 85% of the new car sales.
Currently, Brazil is ranked No2 in the world, in terms of ethanol production, and consequently its motorists enjoy the low cost of ethanol, which is priced at 40% less than gasoline. As well as lower fuel costs, the industrial product tax (purchase tax) on new flex vehicles is only 11%, 2% lower than gasoline models.
The newly-introduced Soul Flex, with its unique exterior design features, boasts a 44% improvement in fuel efficiency compared with the existing gasoline model and superior power (128 ps) and torque (16.5 kg-m) outputs, which are improved by 3.2% and 3.7% respectively from the original model (Table-1).
Differences from the gasoline model include the newly adapted fuel injection & catalyst system as well as engine compression ratio – changes which combine to achieve enhanced fuel economy.
Changes made to accommodate the more abrasive nature of ethanol fuel include reinforcing the fuel pump, pillar cap and fuel line, and fitting a gasoline tank assistance system in order to aid engine ignition at low temperatures.
Kia Motors will begin exporting Soul Flex to Brazil this month, with the new models going on sale at Kia dealerships early next year. Kia is planning to introduce an all-new Sportage 'Flex' model at the end of next year, and Kia will further strengthen its presence in Brazilian market as new flex models are to be introduced in each market segment.
So far in 2010, Brazil has been one of Kia's best performing markets, with sales increasing by 151% year-on-year, reaching 40,865 units up to the end of September.
To strengthen its current sales momentum, Kia plans to take advantage of its involvement with 2014 Brazil FIFA World Cup from the early stages, as a major sponsor of the world's biggest sporting event.
Maximizing the impact of this sponsorship and the introduction of new models, such as Flex models and new SUVs tailored to suit local consumer demands, Kia plans to expand its sales volume in Brazil as well as Central & South American market.
Kia's Soul Flex is the first Korean FFV (Flexible Fuel Vehicle) which can run on an ethanol-gasoline mixture, 100% ethanol or 100% gasoline. It is especially designed for the Brazilian market, where 'flex' models account for more than 85% of the new car sales.
Currently, Brazil is ranked No2 in the world, in terms of ethanol production, and consequently its motorists enjoy the low cost of ethanol, which is priced at 40% less than gasoline. As well as lower fuel costs, the industrial product tax (purchase tax) on new flex vehicles is only 11%, 2% lower than gasoline models.
The newly-introduced Soul Flex, with its unique exterior design features, boasts a 44% improvement in fuel efficiency compared with the existing gasoline model and superior power (128 ps) and torque (16.5 kg-m) outputs, which are improved by 3.2% and 3.7% respectively from the original model (Table-1).
Differences from the gasoline model include the newly adapted fuel injection & catalyst system as well as engine compression ratio – changes which combine to achieve enhanced fuel economy.
Changes made to accommodate the more abrasive nature of ethanol fuel include reinforcing the fuel pump, pillar cap and fuel line, and fitting a gasoline tank assistance system in order to aid engine ignition at low temperatures.
Kia Motors will begin exporting Soul Flex to Brazil this month, with the new models going on sale at Kia dealerships early next year. Kia is planning to introduce an all-new Sportage 'Flex' model at the end of next year, and Kia will further strengthen its presence in Brazilian market as new flex models are to be introduced in each market segment.
So far in 2010, Brazil has been one of Kia's best performing markets, with sales increasing by 151% year-on-year, reaching 40,865 units up to the end of September.
To strengthen its current sales momentum, Kia plans to take advantage of its involvement with 2014 Brazil FIFA World Cup from the early stages, as a major sponsor of the world's biggest sporting event.
Maximizing the impact of this sponsorship and the introduction of new models, such as Flex models and new SUVs tailored to suit local consumer demands, Kia plans to expand its sales volume in Brazil as well as Central & South American market.
FORD TO INVEST ADDITIONAL $850 MILLION IN MICHIGAN TO ENGINEER, BUILD FUEL-EFFICIENT NEW VEHICLES
Workers at Ford's Van Dyke Transmission Plant in Sterling Heights, Mich., assemble fuel-efficient four- and six-speed transmissions for several vehicles in Ford's product lineup. The plant will expand its operations in the next few years as part of Ford's $850 million investment in the state.
* Ford will invest an incremental $850 million in Michigan between 2011 and 2013 as part of its competitive plan to engineer and manufacture even more fuel-efficient vehicles and fuel-saving technologies in the state
* Among other projects, Ford will expand manufacturing capabilities for new, fuel-efficient six-speed transmissions. New investments support up to 1,200 new full-time manufacturing and engineering positions in Michigan
* To help enable this investment plan, Ford has worked with the State of Michigan on job retention tax incentives that contribute to the state's overall manufacturing competitiveness
DETROIT, Oct. 25, 2010 – Ford Motor Company today announced plans to invest an additional $850 million in Michigan between 2011 and 2013 as part of the company's commitment to competitively grow its engineering and manufacturing employee base, upgrade its facilities in the state and further improve its vehicle fuel economy.
"Fuel economy and technology are consumers' biggest priorities – and we have made them Ford's as well," said Mark Fields, Ford's president of The Americas. "We are pleased to work with state and local government leaders to find new ways to work together, invest in our people as well as Ford facilities, further improve our competitiveness and secure jobs in Michigan."
Ford's investment will generate up to 1,200 new full-time positions in manufacturing and engineering operations in Michigan by 2013. The company expects approximately 900 jobs will be hourly positions in its Michigan manufacturing facilities and the remaining 300 will be salaried positions within its engineering and manufacturing operations.
Ford is making the Michigan investment commitment after working with officials on a new Michigan Economic Growth Authority (MEGA) package that replaces several existing state incentives and makes Michigan a more competitive place to invest in new fuel-saving technologies and facilities. The Michigan Economic Development Council considers the package this week.
Once approved, Ford will allocate its $850 million investment across a variety of plants including Van Dyke Transmission, Sterling Axle, Livonia Transmission and Dearborn Truck Plant.
For instance, a significant portion of the company's additional investment will benefit engineering and production of Ford's new six-speed transmissions, which are planned for many future Ford vehicles and built at the Livonia Transmission Plant and Van Dyke Transmission Plant. By 2013, 100 percent of Ford vehicles will incorporate a six-speed transmission as part of the company's commitment to leadership in fuel economy performance in all vehicle segments.
"We applaud the State of Michigan's leadership in finding innovative solutions aimed at making both the state and Ford more competitive," Fields said. "Promoting investments in technologies, facilities and our workforce ultimately will help revitalize manufacturing in Michigan and help Ford compete with the best in the business world-wide."
This most recent investment commitment builds on the $950 million the company previously announced in Michigan to transform the Michigan Assembly Plant from a large SUV factory to a state-of-the-art car plant, which will build the new Focus arriving in showrooms early next year, as well as the company's battery electric Focus and next generation hybrid and plug-in hybrid vehicles, all planned for production at the Wayne, Mich., facility by 2012.
"We've worked hard to keep Michigan the center of the automobile industry, and Ford's investment is further evidence that our efforts are succeeding," said Governor Jennifer M. Granholm. "We look forward to continuing our partnership with Ford as the American auto industry builds the green vehicles of the future."
* Ford will invest an incremental $850 million in Michigan between 2011 and 2013 as part of its competitive plan to engineer and manufacture even more fuel-efficient vehicles and fuel-saving technologies in the state
* Among other projects, Ford will expand manufacturing capabilities for new, fuel-efficient six-speed transmissions. New investments support up to 1,200 new full-time manufacturing and engineering positions in Michigan
* To help enable this investment plan, Ford has worked with the State of Michigan on job retention tax incentives that contribute to the state's overall manufacturing competitiveness
DETROIT, Oct. 25, 2010 – Ford Motor Company today announced plans to invest an additional $850 million in Michigan between 2011 and 2013 as part of the company's commitment to competitively grow its engineering and manufacturing employee base, upgrade its facilities in the state and further improve its vehicle fuel economy.
"Fuel economy and technology are consumers' biggest priorities – and we have made them Ford's as well," said Mark Fields, Ford's president of The Americas. "We are pleased to work with state and local government leaders to find new ways to work together, invest in our people as well as Ford facilities, further improve our competitiveness and secure jobs in Michigan."
Ford's investment will generate up to 1,200 new full-time positions in manufacturing and engineering operations in Michigan by 2013. The company expects approximately 900 jobs will be hourly positions in its Michigan manufacturing facilities and the remaining 300 will be salaried positions within its engineering and manufacturing operations.
Ford is making the Michigan investment commitment after working with officials on a new Michigan Economic Growth Authority (MEGA) package that replaces several existing state incentives and makes Michigan a more competitive place to invest in new fuel-saving technologies and facilities. The Michigan Economic Development Council considers the package this week.
Once approved, Ford will allocate its $850 million investment across a variety of plants including Van Dyke Transmission, Sterling Axle, Livonia Transmission and Dearborn Truck Plant.
For instance, a significant portion of the company's additional investment will benefit engineering and production of Ford's new six-speed transmissions, which are planned for many future Ford vehicles and built at the Livonia Transmission Plant and Van Dyke Transmission Plant. By 2013, 100 percent of Ford vehicles will incorporate a six-speed transmission as part of the company's commitment to leadership in fuel economy performance in all vehicle segments.
"We applaud the State of Michigan's leadership in finding innovative solutions aimed at making both the state and Ford more competitive," Fields said. "Promoting investments in technologies, facilities and our workforce ultimately will help revitalize manufacturing in Michigan and help Ford compete with the best in the business world-wide."
This most recent investment commitment builds on the $950 million the company previously announced in Michigan to transform the Michigan Assembly Plant from a large SUV factory to a state-of-the-art car plant, which will build the new Focus arriving in showrooms early next year, as well as the company's battery electric Focus and next generation hybrid and plug-in hybrid vehicles, all planned for production at the Wayne, Mich., facility by 2012.
"We've worked hard to keep Michigan the center of the automobile industry, and Ford's investment is further evidence that our efforts are succeeding," said Governor Jennifer M. Granholm. "We look forward to continuing our partnership with Ford as the American auto industry builds the green vehicles of the future."
Jun 3, 2010
Ford Motor Company is partnering with Coulomb Technologies to provide free in-home ChargePoint
Ford Motor Company will partner with Coulomb Technologies to provide nearly 5,000 free in-home charging stations for some of the automaker's first electric vehicle customers.
Under the Ford Blue Oval ChargePoint Program, residents in nine designated markets could receive a free ChargePoint® Networked Charging Station with the purchase of a Ford Transit Connect Electric vehicle. The nine markets designated by Coulomb Technologies include Austin, Detroit, Los Angeles, New York, Orlando, Sacramento, the San Jose/San Francisco Bay Area, Redmond, Wash., and Washington D.C. The installation of ChargePoint charging stations will begin immediately.
The Ford Blue Oval ChargePoint Program is part of Coulomb Technologies' $37 million ChargePoint America charging station infrastructure project made possible by a $15 million grant funded by the American Recovery and Reinvestment Act through the Transportation Electrification Initiative administered by the Department of Energy.
"Both the ChargePoint America and Ford Blue Oval ChargePoint Programs help build the necessary infrastructure to make the electric vehicle a more viable option for American consumers," said Sue Cischke, global vice president, Sustainability, Environment and Safety Engineering, Ford Motor Company. "Ford's electrification strategy focuses on providing real world value to customers with a range of driving behaviors and conditions. These programs and charging stations help us deliver an added value to our future electric vehicle owners."
Ford plans to introduce five new electrified vehicles in North America by 2012, providing a range of products to meet a variety of customer needs. These include:
A Transit Connect Electric small commercial van debuting later this year
A Ford Focus Electric passenger car debuting in 2011
Two next-generation lithium-ion battery hybrid-electric vehicles and a plug-in hybrid by 2012.
ChargePoint America will offer home and public charging stations to individuals and businesses. Businesses interested in applying for free public charging stations or consumers exploring an electric vehicle purchase can visit www.chargepointamerica.com for more information.
"ChargePoint America builds upon our established and growing network of charging stations and will in turn encourage consumers to buy electric vehicles," said Richard Lowenthal, CEO of Coulomb Technologies. "Our Department of Energy grant was funded by the American Recovery and Reinvestment Act, also known as the stimulus bill, to provide jobs for Americans. Our products are built and installed with American labor. Every time we ship a ChargePoint charging station, three Americans go to work for a day."
Coulomb's ChargePoint® Network, is open to all plug-in electric vehicle drivers and provides authentication, management and real-time control for the networked electric vehicle charging stations. The network of electric vehicle charging stations is accessible to all plug-in drivers by making a toll-free call to the 24/7 number on each charging station, or signing up for a ChargePoint Network monthly access plan and obtaining a ChargePass™ smart card. Other future payment options include using any smart (RFID) credit/debit card to authorize a session or using a standard credit or debit card at a remote payment station (RPS) to pay for charging sessions. To locate available charging stations, visit mychargepoint.net and click "Find Stations."
Under the Ford Blue Oval ChargePoint Program, residents in nine designated markets could receive a free ChargePoint® Networked Charging Station with the purchase of a Ford Transit Connect Electric vehicle. The nine markets designated by Coulomb Technologies include Austin, Detroit, Los Angeles, New York, Orlando, Sacramento, the San Jose/San Francisco Bay Area, Redmond, Wash., and Washington D.C. The installation of ChargePoint charging stations will begin immediately.
The Ford Blue Oval ChargePoint Program is part of Coulomb Technologies' $37 million ChargePoint America charging station infrastructure project made possible by a $15 million grant funded by the American Recovery and Reinvestment Act through the Transportation Electrification Initiative administered by the Department of Energy.
"Both the ChargePoint America and Ford Blue Oval ChargePoint Programs help build the necessary infrastructure to make the electric vehicle a more viable option for American consumers," said Sue Cischke, global vice president, Sustainability, Environment and Safety Engineering, Ford Motor Company. "Ford's electrification strategy focuses on providing real world value to customers with a range of driving behaviors and conditions. These programs and charging stations help us deliver an added value to our future electric vehicle owners."
Ford plans to introduce five new electrified vehicles in North America by 2012, providing a range of products to meet a variety of customer needs. These include:
A Transit Connect Electric small commercial van debuting later this year
A Ford Focus Electric passenger car debuting in 2011
Two next-generation lithium-ion battery hybrid-electric vehicles and a plug-in hybrid by 2012.
ChargePoint America will offer home and public charging stations to individuals and businesses. Businesses interested in applying for free public charging stations or consumers exploring an electric vehicle purchase can visit www.chargepointamerica.com for more information.
"ChargePoint America builds upon our established and growing network of charging stations and will in turn encourage consumers to buy electric vehicles," said Richard Lowenthal, CEO of Coulomb Technologies. "Our Department of Energy grant was funded by the American Recovery and Reinvestment Act, also known as the stimulus bill, to provide jobs for Americans. Our products are built and installed with American labor. Every time we ship a ChargePoint charging station, three Americans go to work for a day."
Coulomb's ChargePoint® Network, is open to all plug-in electric vehicle drivers and provides authentication, management and real-time control for the networked electric vehicle charging stations. The network of electric vehicle charging stations is accessible to all plug-in drivers by making a toll-free call to the 24/7 number on each charging station, or signing up for a ChargePoint Network monthly access plan and obtaining a ChargePass™ smart card. Other future payment options include using any smart (RFID) credit/debit card to authorize a session or using a standard credit or debit card at a remote payment station (RPS) to pay for charging sessions. To locate available charging stations, visit mychargepoint.net and click "Find Stations."
May 15, 2010
Fiscal Year 2009 Financial Results Press conference Carlos Ghosn, President and CEO, Nissan Motor Co., Ltd. Toshiyuki Shiga, Chief Operating Officer
Carlos Ghosn:
Fiscal year 2009 was an extremely challenging year. At no other time in history has the global automotive industry faced such threatening impacts from the financial crisis, widespread economic recession, a distressed supply base and volatile foreign exchange rates. Within Nissan, we have kept our focus on recovery, guided by our recovery plan. Though we are still operating in crisis mode, we are well on track toward complete recovery. At the close of fiscal year 2009, our consolidated net revenues reached 7.517 trillion yen. Full-year operating profits reached 311.6 billion yen, and net income amounted to 42.4 billion yen. Free cash flow for our auto business resulted in a positive 375.5 billion yen. As a result, net debt for the auto business was reduced to 29.7 billion yen, showing a significant improvement compared to last year's level of 387.9 billion yen. Our core business benefited from the launch of eight all-new models globally, and customers responded positively to our product offer. Consequently, Nissan maintained or increased its market share in Japan, Europe and the United States, and our sales in China increased substantially. As we managed through the financial crisis and recession, Nissan did not compromise its strategic priorities. We did not slow our investments to contribute to a zero-emission society. When the Nissan LEAF goes on sale this year - as the first of the eight all-electric models to launch - the Renault-Nissan Alliance will be the first to mass-market affordable zero-emission vehicles, backed by battery capacity of 500,000 units. No other automaker will be producing electric batteries or cars at such a scale. And customers are ready. To date, 130,000 consumers in the U.S. have registered their interest in buying a Nissan LEAF. With sales starting this December, 13,000 pre-orders have been submitted in just over one month in the U.S. and Japan, largely driven by individual customer demand. This amount already surpasses our available production capacity for fiscal year 2010. Another focus of investments has been our emphasis on very affordable transportation. Entry segments today account for more than 25% of the global TIV of 64 million units, and the segment is growing. We will offer maximum value at affordable prices, beginning with a lineup of global compact cars based on Nissan's new V-platform, which will represent 1 million unit sales at full launch. Importantly, these compact cars' new engines will make eco-friendliness accessible to everyone as they set a new standard for fuel efficiency worldwide. Nissan is moving forward with many actions in emerging markets:
• In China, we will be able to produce more than 1 million cars a year in 2012, based on two shifts at our Huadu, Xiangfang and Zhengzhou plants, and we will expand our capacity further in line with market growth. Our intention is to grow our market share from 6% today to 10% as soon as possible.
• Our Alliance plant in Chennai, India, has started production with a 200,000-unit capacity and plans to increase to 400,000 units at full ramp-up in order to supply the Indian market and to export to more than 100 countries in Europe, Africa and the Middle East. We are also partnering with Ashok Leyland to start LCV production and with Bajaj for an Alliance ultra-low-cost car.
• In Brazil, where TIV grew by 16% this year, our market share stood at less than 1%. Through our growing product portfolio and network coverage, we plan to achieve 5% share in the midterm, contributing to the Alliance share objective of more than 10%.
• In Russia, we will introduce the Murano in early 2011 in our new St. Petersburg factory, in addition to the X-TRAIL and Teana. Nissan's market share stands at 4% today. Using Renault and Avtovaz platforms and production sites and optimizing our capacity, the Renault, Nissan and Avtovaz market share will increase from one-third to 40% as the Russian market recovers.
• In the Middle East, we are on the offensive in GCC with a revitalized network of national sales companies and distributors and the introduction of our large SUV flagship, the all-new Nissan Patrol.
• We are also positioning ourselves for the next wave of emerging countries, such as Indonesia.
Going forward, we believe 2010 will be another difficult year. Global economic conditions are improving, but they are not yet robust. Consumer spending still reflects a shaky confidence in most Western markets as well as in Japan. Commodity prices will be rising with economic recovery. We know the worst of the crisis is behind us, and our plan of action is to emerge from the crisis completely in this fiscal year and start a new mid-term plan in fiscal year 2011. Nissan is heading in the right direction, and we are eager to move forward with clear priorities.
Toshiyuki Shiga:
I will begin the summary of our performance during the past year with a review of global sales. The global TIV was 64.1 million units, an increase from the 61.6 million units sold in fiscal year 2008, mainly due to increases coming from government-led stimulus programs around the world and the increased demand in emerging markets, especially in China. Nissan's global sales amounted to 3.515 million units, a 3% increase year-on-year. Our sales evolution was in line with the TIV change in volatile market conditions, and our overall market share was 5.5%. In the fourth quarter alone, global sales totaled 1,010,000 units, up 29.7% from the same period in fiscal 2008. As in the third quarter, the increase was primarily due to the strong growth in China and the recovery in most of the mature markets. We launched eight new models globally, including the PIXO in Europe; Patrol in the Middle East; NV200 Vanette, Fuga and Roox in Japan; Infiniti G Convertible and 370Z Roadster in the United States; and the new March in Thailand, the first in our global compact car series. Let me give the sales breakdown by region. In Japan, supported by the eco-car tax reductions and incentives offered by the government, the TIV increased 3.8% year-on-year. Our sales reached 630,000 units, 2.9% above the previous year. Nissan's market share remained stable at 12.9%. The NECO series of fuel-efficient models contributed to our sales. Serena was the number-one minivan for the second year in a row, and X-TRAIL ranked first in the SUV segment for the third consecutive year. In the United States, the TIV dropped 9.3% to 10.8 million units. We sold 824,000 units, down 3.8%, while our market share increased four-tenths of a percentage point, to 7.6%. In the fourth quarter alone, sales in the U.S. increased 30.6%, resulting in a record market share of 9%, with strong contributions from the sales of Versa and Altima. In Europe, where the TIV decreased 6.4%, we sold 517,000 units, down 2.4% from the prior year, but our market share increased slightly to 2.8%. Government scrap incentives contributed to our sales increase of 24.5% in Western Europe, but the sales gain was offset by the 60.6% decline in sales in Russia. The light commercial vehicle segment in Europe is still in a very tough position, but we were pleased that our NV200 small van was named the "International Van of the Year 2010." In China, our sales grew 38.7% to 756,000 units. Our market share was 6%, down four-tenths of a percentage point from the prior year because our supply could not meet the strong market demand. In the fourth quarter of fiscal year 2009, sales in China increased 48.1% to 214,000 units, thanks to the strong offensive coming from Sylphy, Teana and Livina. Sales in the first quarter of fiscal year 2010 showed continuous growth, increasing 68.2% to 243,200 units. In other markets, sales in Thailand increased 24.2% to 34,600 units, and the March was named the "Most Environmentally Friendly Car of the Year." In the Middle East, sales dropped 19.7% to 179,100 units. In Australia, sales decreased 1.2% to 55,600 units.
FY09 financial performance Recovery plan actions taken to preserve cash and recover profits contributed to our financial performance in fiscal year 2009. Consolidated net revenues decreased 10.9%, to 7.517 trillion yen, which reflects the stronger yen offsetting the increase in sales volume. Consolidated operating profit totaled 311.6 billion yen, compared to a negative 137.9 billion yen in fiscal 2008. Net income reached 42.4 billion yen, compared to a negative 233.7 billion yen in fiscal 2008. Explaining the operating profit variance analysis:
• The 162.5 billion yen negative impact from foreign exchange came from the appreciation of the yen against all currencies. By currency, the majority of this variance was due to the impact of the U.S. dollar at 86 billion yen, the Russian ruble at 28 billion yen, and the Canadian dollar at 14 billion yen.
• The net impact from purchasing cost reduction was a positive 215.4 billion yen. This amount included a positive impact from the decrease in raw material and energy costs by 81 billion yen. Even though the current market price on raw materials is rapidly increasing, the impact on our results was positive in fiscal year 2009.
• Volume and mix produced a positive impact of 26.9 billion yen as a result of the increase in global sales volume. The fourth quarter of fiscal 2009 was positive by 153.1 billion yen due to the volume recovery in most countries.
• The reduction in Marketing and Sales expense was a positive 27.1 billion yen due mainly to savings in fixed expenses, such as advertising. Incentive spending was increased in Europe due to its tough market conditions.
• The provisions for the residual risk on leased vehicles in North America resulted in a positive variance of 141.7 billion yen, including gains on disposal because of improved used-car prices in our lease portfolio.
• R&D costs decreased 64.5 billion yen.
• Sales financing contributed a positive 50.1 billion yen. This was due mainly to better borrowing costs across the globe and lower loss provisions compared to fiscal year 2008.
• The remaining variance was a positive 86.3 billion yen, due mainly to savings in fixed expenses for all areas, including manufacturing costs and G&A expenses, as well as the profit recovery from affiliate companies, such as Jatco.
For the fourth quarter, global production volume totaled 951,000 units. Our flexible production network responded quickly to adjust production volumes in line with demand. Due to careful inventory management, our inventory of new vehicles remains at a low level, at 470,000 units at the end of fiscal year 2009. We continue to manage inventory carefully to limit its impact on our free cash flow.
FY10 outlook Let's move to our outlook for fiscal year 2010. With a TIV assumption of 66 million units, we expect our global sales to reach 3.8 million units, an increase of 8%, and a record level for Nissan. Our market share will stand at 5.8%. Our global production volume is forecast to be 3.75 million units. We will launch 10 new models globally, with more than 10 regional product launches. Our plan includes the launches of:
• Juke, Elgrand, a new minivan and a new minicar in Japan;
• Infiniti QX in the United States, followed by GCC and Russia;
• the NV series of commercial vans and a convertible crossover in the United States, along with the new Quest minivan for both the U.S. and Canadian markets;
• the Nissan LEAF zero-emission car in the United States and Japan, followed by Europe; and
• the second car in our global compact car series: an affordable sedan.
In fiscal year 2010, we will introduce more than 15 new technologies. "Zero emission" and "PURE DRIVE" are the two key pillars of our environment technology. Our zero-emission technologies will be highlighted by the launch of our EV, Nissan LEAF. In addition to EV, for our internal combustion engine vehicles, we will push hard on a range of low-carbon and low-emission technologies called "PURE DRIVE." These advances include Nissan's original hybrid and clean diesels in association with Renault, which will provide greater fuel efficiency. In addition, we are placing low-emission technologies in an increasing number of our new vehicles. For example, we'll apply idle stop to a wider range of models, starting with compact cars. With so many innovative technologies and products to come, 2010 will be a year to reinforce the image of "Nissan of Technology" in our customers' minds.
Each new year brings risks and opportunities. In fiscal 2010, risks include the continuing strong yen, increasing raw material costs, ongoing uncertainty in world markets, and instability and volatility within the euro-zone. Opportunities include a better-than-expected foreign exchange rate, sales increase in emerging markets, acceleration of Alliance synergies with Renault and further strategic cooperation with Daimler. In light of these factors, we have filed our forecast with the Tokyo Stock Exchange, using a foreign exchange rate assumption for the year of 90 yen to the dollar and 120 yen to the euro. For fiscal year 2010, we forecast the following:
• Net revenue is forecast to be 8.2 trillion yen.
• Operating profit is expected to be 350 billion yen.
• Net income is forecast to be 150 billion yen.
• Capital expenditures are expected to reach 360 billion yen.
• R&D expenses will amount to 430 billion yen.
• Free cash flow will be positive.
• Net auto debt will be eliminated at the end of fiscal year 2010.
Operating profit analysis As I said earlier, we expect the environment in the fiscal year 2010 to continue to be very tough. Even so, our operating profit forecast is expected to be better than last year's performance by 38.4 billion yen - from 311.6 billion yen to 350 billion yen - due to several factors:
• The impact from foreign exchange is a negative 30 billion yen, with the U.S. dollar accounting for the majority of this variance.
• The provisions for the residual risk on leased vehicles in North America result in a negative variance of 40 billion yen, due mainly to the gains on disposal in the last fiscal year because of improved used-car prices in our lease portfolio.
• The net impact from purchasing cost reduction is a positive 60 billion yen. This amount includes a negative impact from the significant increase in raw material and energy costs.
• Volume and mix will produce a positive impact of 270 billion yen as a result of the growth in global sales volume.
• The increase of Marketing and Sales expenses is a negative 140 billion yen due to the normalization of fixed expenses, such as advertising, and the rise in incentives as our volume increases.
• R&D costs are expected to increase by 45 billion yen.
• Others are negative 36.6 billion yen, due mainly to an increase in manufacturing costs and a partial normalization of labor costs to a pre-crisis level.
Direction on recovery Ending fiscal year 2009 with better-than-expected results is good, but market conditions are still volatile. Nissan employees continue to be fully engaged in our company's recovery plan. Our efforts are focused around three core pillars - namely, revenue growth, tight cost management and free cash flow generation. Let me describe each one. First is revenue growth. Though some of our volume will always be linked to external factors, such as shifts in TIV, increases in sales volume are also the result of our own internal efforts. In each major market, we have concrete actions to increase market share, leveraging the planned launches of our 10 new models. For example:
• In the United States, dealer network enhancement activities are supporting performance improvement.
• In China, we intend to secure adequate supply to keep pace with the speed of market growth.
• In Europe, we established a Share Improvement Program that includes detailed steps, such as identifying opportunities through internal benchmarking, setting action plans, allocating resources and reviewing progress on a monthly basis. The improved performance that began in the middle of 2009 is continuing.
On an ongoing basis, we monitor our global car-flow situation closely every month, and we look for ways to optimize opportunities. In addition to vehicle sales, we continue to pursue the growth of associated business, such as after-sales, sales financing and OEM business. In fiscal year 2010, teams will be working on enhancing our conversion and accessory business as well as service business... expanding sales financing activities regionally... and developing business deals around vehicles, powertrains and technologies, including IP licensing of Nissan's technical strengths. Second is tight cost management. Cost reduction within the monozukuri team will continue to be the main pillar of our 2010 recovery plan. Our monozukuri functions - Engineering, Purchasing, Manufacturing and Supply Chain Management - will continue to focus on our action plans linked to technical cost reduction, parts diversity and complexity reduction, and change of material usage. For cost reduction and to neutralize foreign exchange volatility, we will continue resourcing vehicles, parts and powertrains and the localization of parts. In addition to monozukuri cost reduction, we will continue our frugal policy in expenses, such as marketing, manufacturing, R&D, overtime, travel and G&A. We will eliminate some unsustainable measures put in place during the crisis, but we will adopt the new mindset related to all expenses, based on our new standards. In other words, some of the measures put in place throughout our company will become the new normal. The third pillar of our plan is free cash flow generation. In fiscal year 2009, we achieved our positive free cash flow objective, driven largely by cash generation from profit and strictly managed working capital, which includes inventory, accounts payable and receivable. In fiscal year 2010, due to the expected increase in sales and additional sourcing from India and Thailand, working capital will have a negative effect on free cash flow. However, we will minimize this impact through continued strict inventory management, such as ongoing complexity reduction. We will also continue to control all major components of free cash flow other than working capital, such as investing activities. By achieving the three core pillars - revenue growth, disciplined cost management and free cash flow generation - Nissan will be able to complete its recovery this year.
Carlos Ghosn:
The strategic actions we have described today not only reflect our long-term vision of Nissan as a global company that creates sustainable value, but they also show our commitment to maximizing total shareholder return. Based on the current state of our business and weighing the risks and opportunities for this year, we are planning to reinstate dividend payments for fiscal year 2010 at 10 yen for the full year: 5 yen for the interim dividend and 5 yen for the year-end dividend. We will elaborate on future dividend policies when we announce our midterm plan. At the foundation of Nissan's strategy lies the Renault-Nissan Alliance, which is now in its 11th year. The Alliance is a constant lever for creating value and improving performance. Supported by the dedicated team within Renault Nissan BV, compared to our objective of 180 billion yen, we achieved 228 billion yen worth of synergies for the Alliance in 2009, contributing to the free cash flow of both companies for their respective fiscal years. Nissan alone achieved 116 billion yen worth of synergies, primarily through pure cost and CAPEX savings as well as cost and CAPEX avoidance. In 2010 the Alliance should generate 120 billion yen in savings in new synergies. If we include carryover of previous years' synergies, the effect on 2010 free cash flow will be more than 240 billion yen for both Renault and Nissan. The scope of synergies will include joint revenue opportunities in addition to cost and CAPEX savings and avoidance. With more upstream involvement in the decision-making process, the Alliance will be able to identify and integrate synergies into the future plans of both companies. The pursuit of synergies is also behind our strategic cooperation with Daimler, with whom the Alliance will work on small cars, powertrain sharing - including Daimler's 4-cylinder gasoline and diesel engines and a 6-cylinder diesel engine for Infiniti - light commercial vehicles, electric vehicles and batteries, and other areas of common interest. The synergies with Daimler have a projected net present value of at least 2 billion euros for the Alliance. The Renault-Nissan Alliance has established an effective model within our industry. We have shown how large, complex organizations can work together to use scale effectively while maintaining separate corporate identities and autonomy of action. We have demonstrated that strategic partnerships allow each partner to realize more opportunities than either could ever achieve on its own. The synergies Nissan achieves with Renault and, now, with Daimler will contribute to our company's complete recovery and enable future growth. This means growing and being sustainable in a new era that requires meeting the growing demand for affordable mobility while being conscious of and responsive to environmental requirements. A year ago, I said Nissan knows how to adapt and face a crisis. Today, you can see how we have progressed and where we are headed. The lessons learned from our revival experience in 1999 and our recovery actions in 2009 are now built or being built into our global business practices. We will emerge from this crisis more competitive and stronger. Our commitment to our customers and our stakeholders is that - no matter what the obstacles - you can expect the best from Nissan.
Fiscal year 2009 was an extremely challenging year. At no other time in history has the global automotive industry faced such threatening impacts from the financial crisis, widespread economic recession, a distressed supply base and volatile foreign exchange rates. Within Nissan, we have kept our focus on recovery, guided by our recovery plan. Though we are still operating in crisis mode, we are well on track toward complete recovery. At the close of fiscal year 2009, our consolidated net revenues reached 7.517 trillion yen. Full-year operating profits reached 311.6 billion yen, and net income amounted to 42.4 billion yen. Free cash flow for our auto business resulted in a positive 375.5 billion yen. As a result, net debt for the auto business was reduced to 29.7 billion yen, showing a significant improvement compared to last year's level of 387.9 billion yen. Our core business benefited from the launch of eight all-new models globally, and customers responded positively to our product offer. Consequently, Nissan maintained or increased its market share in Japan, Europe and the United States, and our sales in China increased substantially. As we managed through the financial crisis and recession, Nissan did not compromise its strategic priorities. We did not slow our investments to contribute to a zero-emission society. When the Nissan LEAF goes on sale this year - as the first of the eight all-electric models to launch - the Renault-Nissan Alliance will be the first to mass-market affordable zero-emission vehicles, backed by battery capacity of 500,000 units. No other automaker will be producing electric batteries or cars at such a scale. And customers are ready. To date, 130,000 consumers in the U.S. have registered their interest in buying a Nissan LEAF. With sales starting this December, 13,000 pre-orders have been submitted in just over one month in the U.S. and Japan, largely driven by individual customer demand. This amount already surpasses our available production capacity for fiscal year 2010. Another focus of investments has been our emphasis on very affordable transportation. Entry segments today account for more than 25% of the global TIV of 64 million units, and the segment is growing. We will offer maximum value at affordable prices, beginning with a lineup of global compact cars based on Nissan's new V-platform, which will represent 1 million unit sales at full launch. Importantly, these compact cars' new engines will make eco-friendliness accessible to everyone as they set a new standard for fuel efficiency worldwide. Nissan is moving forward with many actions in emerging markets:
• In China, we will be able to produce more than 1 million cars a year in 2012, based on two shifts at our Huadu, Xiangfang and Zhengzhou plants, and we will expand our capacity further in line with market growth. Our intention is to grow our market share from 6% today to 10% as soon as possible.
• Our Alliance plant in Chennai, India, has started production with a 200,000-unit capacity and plans to increase to 400,000 units at full ramp-up in order to supply the Indian market and to export to more than 100 countries in Europe, Africa and the Middle East. We are also partnering with Ashok Leyland to start LCV production and with Bajaj for an Alliance ultra-low-cost car.
• In Brazil, where TIV grew by 16% this year, our market share stood at less than 1%. Through our growing product portfolio and network coverage, we plan to achieve 5% share in the midterm, contributing to the Alliance share objective of more than 10%.
• In Russia, we will introduce the Murano in early 2011 in our new St. Petersburg factory, in addition to the X-TRAIL and Teana. Nissan's market share stands at 4% today. Using Renault and Avtovaz platforms and production sites and optimizing our capacity, the Renault, Nissan and Avtovaz market share will increase from one-third to 40% as the Russian market recovers.
• In the Middle East, we are on the offensive in GCC with a revitalized network of national sales companies and distributors and the introduction of our large SUV flagship, the all-new Nissan Patrol.
• We are also positioning ourselves for the next wave of emerging countries, such as Indonesia.
Going forward, we believe 2010 will be another difficult year. Global economic conditions are improving, but they are not yet robust. Consumer spending still reflects a shaky confidence in most Western markets as well as in Japan. Commodity prices will be rising with economic recovery. We know the worst of the crisis is behind us, and our plan of action is to emerge from the crisis completely in this fiscal year and start a new mid-term plan in fiscal year 2011. Nissan is heading in the right direction, and we are eager to move forward with clear priorities.
Toshiyuki Shiga:
I will begin the summary of our performance during the past year with a review of global sales. The global TIV was 64.1 million units, an increase from the 61.6 million units sold in fiscal year 2008, mainly due to increases coming from government-led stimulus programs around the world and the increased demand in emerging markets, especially in China. Nissan's global sales amounted to 3.515 million units, a 3% increase year-on-year. Our sales evolution was in line with the TIV change in volatile market conditions, and our overall market share was 5.5%. In the fourth quarter alone, global sales totaled 1,010,000 units, up 29.7% from the same period in fiscal 2008. As in the third quarter, the increase was primarily due to the strong growth in China and the recovery in most of the mature markets. We launched eight new models globally, including the PIXO in Europe; Patrol in the Middle East; NV200 Vanette, Fuga and Roox in Japan; Infiniti G Convertible and 370Z Roadster in the United States; and the new March in Thailand, the first in our global compact car series. Let me give the sales breakdown by region. In Japan, supported by the eco-car tax reductions and incentives offered by the government, the TIV increased 3.8% year-on-year. Our sales reached 630,000 units, 2.9% above the previous year. Nissan's market share remained stable at 12.9%. The NECO series of fuel-efficient models contributed to our sales. Serena was the number-one minivan for the second year in a row, and X-TRAIL ranked first in the SUV segment for the third consecutive year. In the United States, the TIV dropped 9.3% to 10.8 million units. We sold 824,000 units, down 3.8%, while our market share increased four-tenths of a percentage point, to 7.6%. In the fourth quarter alone, sales in the U.S. increased 30.6%, resulting in a record market share of 9%, with strong contributions from the sales of Versa and Altima. In Europe, where the TIV decreased 6.4%, we sold 517,000 units, down 2.4% from the prior year, but our market share increased slightly to 2.8%. Government scrap incentives contributed to our sales increase of 24.5% in Western Europe, but the sales gain was offset by the 60.6% decline in sales in Russia. The light commercial vehicle segment in Europe is still in a very tough position, but we were pleased that our NV200 small van was named the "International Van of the Year 2010." In China, our sales grew 38.7% to 756,000 units. Our market share was 6%, down four-tenths of a percentage point from the prior year because our supply could not meet the strong market demand. In the fourth quarter of fiscal year 2009, sales in China increased 48.1% to 214,000 units, thanks to the strong offensive coming from Sylphy, Teana and Livina. Sales in the first quarter of fiscal year 2010 showed continuous growth, increasing 68.2% to 243,200 units. In other markets, sales in Thailand increased 24.2% to 34,600 units, and the March was named the "Most Environmentally Friendly Car of the Year." In the Middle East, sales dropped 19.7% to 179,100 units. In Australia, sales decreased 1.2% to 55,600 units.
FY09 financial performance Recovery plan actions taken to preserve cash and recover profits contributed to our financial performance in fiscal year 2009. Consolidated net revenues decreased 10.9%, to 7.517 trillion yen, which reflects the stronger yen offsetting the increase in sales volume. Consolidated operating profit totaled 311.6 billion yen, compared to a negative 137.9 billion yen in fiscal 2008. Net income reached 42.4 billion yen, compared to a negative 233.7 billion yen in fiscal 2008. Explaining the operating profit variance analysis:
• The 162.5 billion yen negative impact from foreign exchange came from the appreciation of the yen against all currencies. By currency, the majority of this variance was due to the impact of the U.S. dollar at 86 billion yen, the Russian ruble at 28 billion yen, and the Canadian dollar at 14 billion yen.
• The net impact from purchasing cost reduction was a positive 215.4 billion yen. This amount included a positive impact from the decrease in raw material and energy costs by 81 billion yen. Even though the current market price on raw materials is rapidly increasing, the impact on our results was positive in fiscal year 2009.
• Volume and mix produced a positive impact of 26.9 billion yen as a result of the increase in global sales volume. The fourth quarter of fiscal 2009 was positive by 153.1 billion yen due to the volume recovery in most countries.
• The reduction in Marketing and Sales expense was a positive 27.1 billion yen due mainly to savings in fixed expenses, such as advertising. Incentive spending was increased in Europe due to its tough market conditions.
• The provisions for the residual risk on leased vehicles in North America resulted in a positive variance of 141.7 billion yen, including gains on disposal because of improved used-car prices in our lease portfolio.
• R&D costs decreased 64.5 billion yen.
• Sales financing contributed a positive 50.1 billion yen. This was due mainly to better borrowing costs across the globe and lower loss provisions compared to fiscal year 2008.
• The remaining variance was a positive 86.3 billion yen, due mainly to savings in fixed expenses for all areas, including manufacturing costs and G&A expenses, as well as the profit recovery from affiliate companies, such as Jatco.
For the fourth quarter, global production volume totaled 951,000 units. Our flexible production network responded quickly to adjust production volumes in line with demand. Due to careful inventory management, our inventory of new vehicles remains at a low level, at 470,000 units at the end of fiscal year 2009. We continue to manage inventory carefully to limit its impact on our free cash flow.
FY10 outlook Let's move to our outlook for fiscal year 2010. With a TIV assumption of 66 million units, we expect our global sales to reach 3.8 million units, an increase of 8%, and a record level for Nissan. Our market share will stand at 5.8%. Our global production volume is forecast to be 3.75 million units. We will launch 10 new models globally, with more than 10 regional product launches. Our plan includes the launches of:
• Juke, Elgrand, a new minivan and a new minicar in Japan;
• Infiniti QX in the United States, followed by GCC and Russia;
• the NV series of commercial vans and a convertible crossover in the United States, along with the new Quest minivan for both the U.S. and Canadian markets;
• the Nissan LEAF zero-emission car in the United States and Japan, followed by Europe; and
• the second car in our global compact car series: an affordable sedan.
In fiscal year 2010, we will introduce more than 15 new technologies. "Zero emission" and "PURE DRIVE" are the two key pillars of our environment technology. Our zero-emission technologies will be highlighted by the launch of our EV, Nissan LEAF. In addition to EV, for our internal combustion engine vehicles, we will push hard on a range of low-carbon and low-emission technologies called "PURE DRIVE." These advances include Nissan's original hybrid and clean diesels in association with Renault, which will provide greater fuel efficiency. In addition, we are placing low-emission technologies in an increasing number of our new vehicles. For example, we'll apply idle stop to a wider range of models, starting with compact cars. With so many innovative technologies and products to come, 2010 will be a year to reinforce the image of "Nissan of Technology" in our customers' minds.
Each new year brings risks and opportunities. In fiscal 2010, risks include the continuing strong yen, increasing raw material costs, ongoing uncertainty in world markets, and instability and volatility within the euro-zone. Opportunities include a better-than-expected foreign exchange rate, sales increase in emerging markets, acceleration of Alliance synergies with Renault and further strategic cooperation with Daimler. In light of these factors, we have filed our forecast with the Tokyo Stock Exchange, using a foreign exchange rate assumption for the year of 90 yen to the dollar and 120 yen to the euro. For fiscal year 2010, we forecast the following:
• Net revenue is forecast to be 8.2 trillion yen.
• Operating profit is expected to be 350 billion yen.
• Net income is forecast to be 150 billion yen.
• Capital expenditures are expected to reach 360 billion yen.
• R&D expenses will amount to 430 billion yen.
• Free cash flow will be positive.
• Net auto debt will be eliminated at the end of fiscal year 2010.
Operating profit analysis As I said earlier, we expect the environment in the fiscal year 2010 to continue to be very tough. Even so, our operating profit forecast is expected to be better than last year's performance by 38.4 billion yen - from 311.6 billion yen to 350 billion yen - due to several factors:
• The impact from foreign exchange is a negative 30 billion yen, with the U.S. dollar accounting for the majority of this variance.
• The provisions for the residual risk on leased vehicles in North America result in a negative variance of 40 billion yen, due mainly to the gains on disposal in the last fiscal year because of improved used-car prices in our lease portfolio.
• The net impact from purchasing cost reduction is a positive 60 billion yen. This amount includes a negative impact from the significant increase in raw material and energy costs.
• Volume and mix will produce a positive impact of 270 billion yen as a result of the growth in global sales volume.
• The increase of Marketing and Sales expenses is a negative 140 billion yen due to the normalization of fixed expenses, such as advertising, and the rise in incentives as our volume increases.
• R&D costs are expected to increase by 45 billion yen.
• Others are negative 36.6 billion yen, due mainly to an increase in manufacturing costs and a partial normalization of labor costs to a pre-crisis level.
Direction on recovery Ending fiscal year 2009 with better-than-expected results is good, but market conditions are still volatile. Nissan employees continue to be fully engaged in our company's recovery plan. Our efforts are focused around three core pillars - namely, revenue growth, tight cost management and free cash flow generation. Let me describe each one. First is revenue growth. Though some of our volume will always be linked to external factors, such as shifts in TIV, increases in sales volume are also the result of our own internal efforts. In each major market, we have concrete actions to increase market share, leveraging the planned launches of our 10 new models. For example:
• In the United States, dealer network enhancement activities are supporting performance improvement.
• In China, we intend to secure adequate supply to keep pace with the speed of market growth.
• In Europe, we established a Share Improvement Program that includes detailed steps, such as identifying opportunities through internal benchmarking, setting action plans, allocating resources and reviewing progress on a monthly basis. The improved performance that began in the middle of 2009 is continuing.
On an ongoing basis, we monitor our global car-flow situation closely every month, and we look for ways to optimize opportunities. In addition to vehicle sales, we continue to pursue the growth of associated business, such as after-sales, sales financing and OEM business. In fiscal year 2010, teams will be working on enhancing our conversion and accessory business as well as service business... expanding sales financing activities regionally... and developing business deals around vehicles, powertrains and technologies, including IP licensing of Nissan's technical strengths. Second is tight cost management. Cost reduction within the monozukuri team will continue to be the main pillar of our 2010 recovery plan. Our monozukuri functions - Engineering, Purchasing, Manufacturing and Supply Chain Management - will continue to focus on our action plans linked to technical cost reduction, parts diversity and complexity reduction, and change of material usage. For cost reduction and to neutralize foreign exchange volatility, we will continue resourcing vehicles, parts and powertrains and the localization of parts. In addition to monozukuri cost reduction, we will continue our frugal policy in expenses, such as marketing, manufacturing, R&D, overtime, travel and G&A. We will eliminate some unsustainable measures put in place during the crisis, but we will adopt the new mindset related to all expenses, based on our new standards. In other words, some of the measures put in place throughout our company will become the new normal. The third pillar of our plan is free cash flow generation. In fiscal year 2009, we achieved our positive free cash flow objective, driven largely by cash generation from profit and strictly managed working capital, which includes inventory, accounts payable and receivable. In fiscal year 2010, due to the expected increase in sales and additional sourcing from India and Thailand, working capital will have a negative effect on free cash flow. However, we will minimize this impact through continued strict inventory management, such as ongoing complexity reduction. We will also continue to control all major components of free cash flow other than working capital, such as investing activities. By achieving the three core pillars - revenue growth, disciplined cost management and free cash flow generation - Nissan will be able to complete its recovery this year.
Carlos Ghosn:
The strategic actions we have described today not only reflect our long-term vision of Nissan as a global company that creates sustainable value, but they also show our commitment to maximizing total shareholder return. Based on the current state of our business and weighing the risks and opportunities for this year, we are planning to reinstate dividend payments for fiscal year 2010 at 10 yen for the full year: 5 yen for the interim dividend and 5 yen for the year-end dividend. We will elaborate on future dividend policies when we announce our midterm plan. At the foundation of Nissan's strategy lies the Renault-Nissan Alliance, which is now in its 11th year. The Alliance is a constant lever for creating value and improving performance. Supported by the dedicated team within Renault Nissan BV, compared to our objective of 180 billion yen, we achieved 228 billion yen worth of synergies for the Alliance in 2009, contributing to the free cash flow of both companies for their respective fiscal years. Nissan alone achieved 116 billion yen worth of synergies, primarily through pure cost and CAPEX savings as well as cost and CAPEX avoidance. In 2010 the Alliance should generate 120 billion yen in savings in new synergies. If we include carryover of previous years' synergies, the effect on 2010 free cash flow will be more than 240 billion yen for both Renault and Nissan. The scope of synergies will include joint revenue opportunities in addition to cost and CAPEX savings and avoidance. With more upstream involvement in the decision-making process, the Alliance will be able to identify and integrate synergies into the future plans of both companies. The pursuit of synergies is also behind our strategic cooperation with Daimler, with whom the Alliance will work on small cars, powertrain sharing - including Daimler's 4-cylinder gasoline and diesel engines and a 6-cylinder diesel engine for Infiniti - light commercial vehicles, electric vehicles and batteries, and other areas of common interest. The synergies with Daimler have a projected net present value of at least 2 billion euros for the Alliance. The Renault-Nissan Alliance has established an effective model within our industry. We have shown how large, complex organizations can work together to use scale effectively while maintaining separate corporate identities and autonomy of action. We have demonstrated that strategic partnerships allow each partner to realize more opportunities than either could ever achieve on its own. The synergies Nissan achieves with Renault and, now, with Daimler will contribute to our company's complete recovery and enable future growth. This means growing and being sustainable in a new era that requires meeting the growing demand for affordable mobility while being conscious of and responsive to environmental requirements. A year ago, I said Nissan knows how to adapt and face a crisis. Today, you can see how we have progressed and where we are headed. The lessons learned from our revival experience in 1999 and our recovery actions in 2009 are now built or being built into our global business practices. We will emerge from this crisis more competitive and stronger. Our commitment to our customers and our stakeholders is that - no matter what the obstacles - you can expect the best from Nissan.
Apr 30, 2010
Audi looks to invest in renewable electricity
AUDI AG is looking to invest in renewable sources of energy. In support of this goal, Audi this week signed an agreement with the international consortium "Desertec Industrial Initiative". The long-term goal of the joint venture is the climate-friendly production of energy in the deserts of North Africa and the Middle East. As an associated partner, Audi will initially work to create the right conditions and to establish the necessary infrastructure.
"When at Audi we speak of sustainable mobility, we are looking at the entire energy balance", said Rupert Stadler, Chairman of the Board of Management of AUDI AG. Audi is looking to introduce its first small-series electric car to the market as early as 2012. In doing so, Stadler said Audi will not only apply the principles of sustainability to the production of the cars, but also to ensure that customers can sustainably operate the cars. "Electric cars from Audi will run on sustainably produced electricity. To achieve this goal we're supporting the development of solar- and wind-driven power plants", Stadler said.
By partnering with Desertec, Audi is joining a unique industrial initiative. It is working to achieve a safe, sustainable and climate-friendly energy supply from the deserts of North Africa and the Middle East. The Desertec Industrial Initiative is working to develop the right conditions for targeted investment in solar and wind energy on the basis of careful analysis. Today the Desertec Industrial Initiative is backed by 16 founding companies, the DESERTEC Foundation and associated partners, who work to support the initiative's objectives.
In its holistic view of the energy balance of its products, AUDI AG includes its production processes. Surpassing the common German mix, an above-average percentage of the energy needed for production is fed into AUDI AG's plants from renewable sources. Novel photovoltaic panels on its roofs actively feed green electricity into the German grid. In the future, roughly an additional 14,000 megawatt hours are to be added to this through wind power; the utilization of biogas is also foreseen. The partnership with Desertec now expands this commitment.
"When at Audi we speak of sustainable mobility, we are looking at the entire energy balance", said Rupert Stadler, Chairman of the Board of Management of AUDI AG. Audi is looking to introduce its first small-series electric car to the market as early as 2012. In doing so, Stadler said Audi will not only apply the principles of sustainability to the production of the cars, but also to ensure that customers can sustainably operate the cars. "Electric cars from Audi will run on sustainably produced electricity. To achieve this goal we're supporting the development of solar- and wind-driven power plants", Stadler said.
By partnering with Desertec, Audi is joining a unique industrial initiative. It is working to achieve a safe, sustainable and climate-friendly energy supply from the deserts of North Africa and the Middle East. The Desertec Industrial Initiative is working to develop the right conditions for targeted investment in solar and wind energy on the basis of careful analysis. Today the Desertec Industrial Initiative is backed by 16 founding companies, the DESERTEC Foundation and associated partners, who work to support the initiative's objectives.
In its holistic view of the energy balance of its products, AUDI AG includes its production processes. Surpassing the common German mix, an above-average percentage of the energy needed for production is fed into AUDI AG's plants from renewable sources. Novel photovoltaic panels on its roofs actively feed green electricity into the German grid. In the future, roughly an additional 14,000 megawatt hours are to be added to this through wind power; the utilization of biogas is also foreseen. The partnership with Desertec now expands this commitment.
Apr 29, 2010
Opel Ampera Passes Production Milestone
The Opel Ampera passed an important milestone Friday, April 23, when the first pre-production Model Year 2012 Ampera rolled off the line at GM's Pre-Production Operations assembly line in Warren, Michigan.
Assembly workers will build more pre-production Amperas in the coming months. These pre-production vehicles will not be sold at dealerships, but used instead for testing and validating the production intent design as well as developing the final vehicle software and controls. Engineers in Europe and the United States also use them to tune the vehicle's overall driving experience. Some of these Amperas will have very short lives as they will be used in safety and structural integrity testing.
"We're right on target for producing the Ampera for European markets later next year," said Andrew Farah, Vehicle Chief Engineer for the Ampera "There's still work to be done, but being able to drive an Opel Ampera off our pre-production line is a great accomplishment for the teams here and in Europe."
The Opel Ampera extended-range electric vehicle delivers up to 60 kilometers of pure electric driving before an engine-generator kicks in to sustain the battery charge and seamlessly extend the range to more than 500 kilometers. The battery can be charged by plugging the vehicle's on-board charge system into a standard household outlet. It is scheduled to go on sale end 2011.
Assembly workers will build more pre-production Amperas in the coming months. These pre-production vehicles will not be sold at dealerships, but used instead for testing and validating the production intent design as well as developing the final vehicle software and controls. Engineers in Europe and the United States also use them to tune the vehicle's overall driving experience. Some of these Amperas will have very short lives as they will be used in safety and structural integrity testing.
"We're right on target for producing the Ampera for European markets later next year," said Andrew Farah, Vehicle Chief Engineer for the Ampera "There's still work to be done, but being able to drive an Opel Ampera off our pre-production line is a great accomplishment for the teams here and in Europe."
The Opel Ampera extended-range electric vehicle delivers up to 60 kilometers of pure electric driving before an engine-generator kicks in to sustain the battery charge and seamlessly extend the range to more than 500 kilometers. The battery can be charged by plugging the vehicle's on-board charge system into a standard household outlet. It is scheduled to go on sale end 2011.
Labels:
chevy volt,
ChevyVolt,
opel,
opel ampera,
OpelAmpera
Apr 22, 2010
Largest gathering of Tesla Roadsters ever
Roadster owners are a fascinating group of people with varied backgrounds and great stories to tell. I’ve had the pleasure of getting to know many of them over the past year delivering cars from our Menlo Park store. After rejoining our headquarters Customer Service team, it’s the daily interaction with our owners I miss most. When asked to help host the March 21st Road Rally for local customers, I didn’t hesitate.
We kicked off the event at the Tesla Store Menlo Park. Once everyone had assembled in the parking lot and enjoyed some coffee and snacks, we had a quick drivers’ meeting and were off. Up Sand Hill Road we went, passing some of the very VCs whose investments made these cars possible in the first place. We hopped on Highway 280, where Roadsters are becoming a familiar sight, then took the 92 towards the coast. Highway 92 is made for the Roadster – its a fun little twisty road that courses over Crystal Springs Reservoir and up into the coastal hills which greet the Pacific fog each evening. From the crest, we made our way down into the sleepy hamlet of Half Moon Bay. We cruised down the coast as the morning fog dissipated, exposing some of the best scenery the Pacific has to offer. After a dozen breathtaking miles on PCH, we stopped at Pomponio State Beach to line up the Roadsters for their photo shoot.
As we pulled in, I tallied up the Roadsters. There were thirty customer cars and four cars from our company fleet. A few of our earliest customers were there touting odometers that read over 20,000 miles. I was driving Validation Prototype 11 which had the highest mileage of any Roadster present, with roughly 67,000 miles on the odometer. Not bad for a car just over two years old! Leading the pack was our beloved VIN 750, the car we watched drive across the country to Detroit for NAIAS in January.
In the parking lot of Pomponio State Beach, we checked out the cars (a great opportunity to see color combos and customizations), and owners traded stories of how they came to be Roadster Owners. We took a group photo to commemorate the largest rally of Roadsters to date (beat that, LA!).
We were able to keep a tight grouping as we motored back up the hills to Skyline Boulevard, the famous ribbon of blacktop running along the hilltop crest of the peninsula south of San Francisco. This crossroads is home to Alice’s Restaurant, a local favorite for anyone who likes to tackle twisty roads on two or four wheels. This was the site of some of our earliest test drives, so this hilltop intersection is certainly a special place for Tesla. As we piled up for the stop sign, we could see restaurant patrons pouring out to have a look and give us a wave. While Roadsters may have become a regular sight in the Bay Area, seeing 34 of them in a row is certainly a spectacle!
After we slid down the hill and made our way into Palo Alto, we pulled into the parking lot of our new Headquarters where lunch was waiting. Since most of the building is still a hardhat zone while we prepare to build electric powertrain components, we ate in the sunshine, discussing the merits of solar power, electric drive, and the special feeling of being a member of the Roadster Owner Community.
I can’t think of a better way of spending a Sunday morning with a Roadster. If you can, let us know, we’re listening.
We kicked off the event at the Tesla Store Menlo Park. Once everyone had assembled in the parking lot and enjoyed some coffee and snacks, we had a quick drivers’ meeting and were off. Up Sand Hill Road we went, passing some of the very VCs whose investments made these cars possible in the first place. We hopped on Highway 280, where Roadsters are becoming a familiar sight, then took the 92 towards the coast. Highway 92 is made for the Roadster – its a fun little twisty road that courses over Crystal Springs Reservoir and up into the coastal hills which greet the Pacific fog each evening. From the crest, we made our way down into the sleepy hamlet of Half Moon Bay. We cruised down the coast as the morning fog dissipated, exposing some of the best scenery the Pacific has to offer. After a dozen breathtaking miles on PCH, we stopped at Pomponio State Beach to line up the Roadsters for their photo shoot.
As we pulled in, I tallied up the Roadsters. There were thirty customer cars and four cars from our company fleet. A few of our earliest customers were there touting odometers that read over 20,000 miles. I was driving Validation Prototype 11 which had the highest mileage of any Roadster present, with roughly 67,000 miles on the odometer. Not bad for a car just over two years old! Leading the pack was our beloved VIN 750, the car we watched drive across the country to Detroit for NAIAS in January.
In the parking lot of Pomponio State Beach, we checked out the cars (a great opportunity to see color combos and customizations), and owners traded stories of how they came to be Roadster Owners. We took a group photo to commemorate the largest rally of Roadsters to date (beat that, LA!).
We were able to keep a tight grouping as we motored back up the hills to Skyline Boulevard, the famous ribbon of blacktop running along the hilltop crest of the peninsula south of San Francisco. This crossroads is home to Alice’s Restaurant, a local favorite for anyone who likes to tackle twisty roads on two or four wheels. This was the site of some of our earliest test drives, so this hilltop intersection is certainly a special place for Tesla. As we piled up for the stop sign, we could see restaurant patrons pouring out to have a look and give us a wave. While Roadsters may have become a regular sight in the Bay Area, seeing 34 of them in a row is certainly a spectacle!
After we slid down the hill and made our way into Palo Alto, we pulled into the parking lot of our new Headquarters where lunch was waiting. Since most of the building is still a hardhat zone while we prepare to build electric powertrain components, we ate in the sunshine, discussing the merits of solar power, electric drive, and the special feeling of being a member of the Roadster Owner Community.
I can’t think of a better way of spending a Sunday morning with a Roadster. If you can, let us know, we’re listening.
Apr 6, 2010
Progressive design for the Audi R15 TDI
Audi wants to surprise the spectators at this year's 24-hour race at Le Mans (France) with a progressive design: the Audi Design Team created a fresh outfit for the innovative diesel race sports car that bears all the hallmarks of "pleasure in efficiency."
Whereas silver was the dominant color of the Audi R15 TDI last year, the 2010 model boasts a radical new design that features more red. In addition, large areas of the Le Mans race sports car that is internally designated as "R15 plus" will be kept in a purist black carbon-fiber look.
"We're happy that we were allowed to give the car such a progressive look," say Markus Auerbach and Tobias Drews from the Audi Design Team. "We wanted to add a dash of surprise when the Audi leaves the pits at Le Mans. We practically opened up the bodywork and are exposing the light-weight construction and its uncompromising technical development - and with a little rock 'n' roll for good measure."
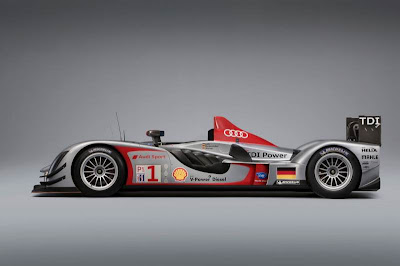
The Audi R15 TDI sporting its new design will make its debut at the Le Castellet 8 Hours on April 11. Audi Sport Team Joest will contest the 2010 season opener of the Le Mans Series in preparation for the Le Mans (France) 24 Hours on June 12/13. Another test race is planned at the 1000-kilometer race at Spa-Francorchamps (Belgium).
"The race at Le Castellet comes at a very early point in time for us and is nothing but a test in racing conditions," stresses Ralf Jüttner, Technical Director of Audi Sport Team Joest. "Even though it's a difficult logistical undertaking, we wanted to gather experiences with the R15 plus at a race as early as possible. Le Castellet offers the opportunity to do this."
The 2010 version of the Audi R15 TDI completed a roll-out at the Audi test track in Neustadt at the beginning of March. The prototype was subsequently flown to the USA for initial tests which primarily featured aerodynamics trials. A five-day endurance test followed at Sebring (Florida) at which about 5 500 kilometers were reeled off without any technical problems worth mentioning.
In Europe, the final set-up work with a view toward Le Mans is on the agenda. Further track tests will now be followed by the first run in a race at which the result will be of secondary importance for Audi though. "Le Castellet will strictly be about gathering additional experience with the R15 plus," emphasizes Head of Audi Motorsport Dr. Wolfgang Ullrich. "Racing conditions simply can't be simulated in normal track tests; that's why we're contesting a race at such an early stage."
It is planned to field the R15 plus with chassis number 202. Audi Sport Team Joest has nominated Dindo Capello (Italy), Tom Kristensen (Denmark) and Allan McNish (Scotland) as drivers. "However, we will only decide whether all three drivers will actually race at short notice," says Dr. Wolfgang Ullrich.
Since Audi has performed several endurance tests for the Le Mans 24 Hours at Le Castellet in recent years, the team and drivers are intimately familiar with the circuit in southern France.
Audi, by the way, has very good memories of its most recent racing commitment at Le Castellet: in 1995, Frank Biela won the Touring Car World Cup there in the Audi A4 quattro against strong rivals.
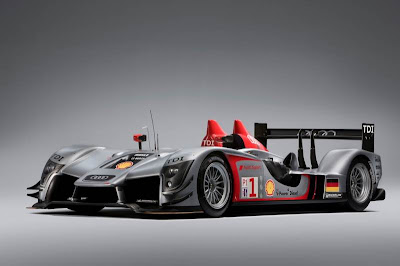
The schedule at Le Castellet
Friday, April 9
12:40–13:40 hrs free practice 1
16:10–17:10 hrs free practice 2
Saturday, April 10
09:45–10:45 hrs free practice 3
13:40–14:00 hrs qualifying (GT vehicles)
14:10–14:30 hrs qualifying (prototypes)
Sunday, April 11
08:20–08:40 hrs warm-up
11:00–19:00 hrs race
Whereas silver was the dominant color of the Audi R15 TDI last year, the 2010 model boasts a radical new design that features more red. In addition, large areas of the Le Mans race sports car that is internally designated as "R15 plus" will be kept in a purist black carbon-fiber look.
"We're happy that we were allowed to give the car such a progressive look," say Markus Auerbach and Tobias Drews from the Audi Design Team. "We wanted to add a dash of surprise when the Audi leaves the pits at Le Mans. We practically opened up the bodywork and are exposing the light-weight construction and its uncompromising technical development - and with a little rock 'n' roll for good measure."
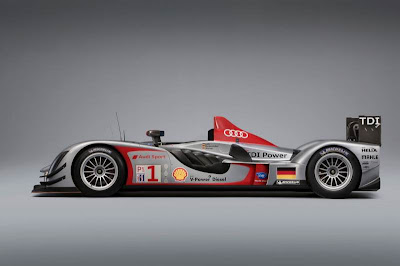
The Audi R15 TDI sporting its new design will make its debut at the Le Castellet 8 Hours on April 11. Audi Sport Team Joest will contest the 2010 season opener of the Le Mans Series in preparation for the Le Mans (France) 24 Hours on June 12/13. Another test race is planned at the 1000-kilometer race at Spa-Francorchamps (Belgium).
"The race at Le Castellet comes at a very early point in time for us and is nothing but a test in racing conditions," stresses Ralf Jüttner, Technical Director of Audi Sport Team Joest. "Even though it's a difficult logistical undertaking, we wanted to gather experiences with the R15 plus at a race as early as possible. Le Castellet offers the opportunity to do this."
The 2010 version of the Audi R15 TDI completed a roll-out at the Audi test track in Neustadt at the beginning of March. The prototype was subsequently flown to the USA for initial tests which primarily featured aerodynamics trials. A five-day endurance test followed at Sebring (Florida) at which about 5 500 kilometers were reeled off without any technical problems worth mentioning.
In Europe, the final set-up work with a view toward Le Mans is on the agenda. Further track tests will now be followed by the first run in a race at which the result will be of secondary importance for Audi though. "Le Castellet will strictly be about gathering additional experience with the R15 plus," emphasizes Head of Audi Motorsport Dr. Wolfgang Ullrich. "Racing conditions simply can't be simulated in normal track tests; that's why we're contesting a race at such an early stage."
It is planned to field the R15 plus with chassis number 202. Audi Sport Team Joest has nominated Dindo Capello (Italy), Tom Kristensen (Denmark) and Allan McNish (Scotland) as drivers. "However, we will only decide whether all three drivers will actually race at short notice," says Dr. Wolfgang Ullrich.
Since Audi has performed several endurance tests for the Le Mans 24 Hours at Le Castellet in recent years, the team and drivers are intimately familiar with the circuit in southern France.
Audi, by the way, has very good memories of its most recent racing commitment at Le Castellet: in 1995, Frank Biela won the Touring Car World Cup there in the Audi A4 quattro against strong rivals.
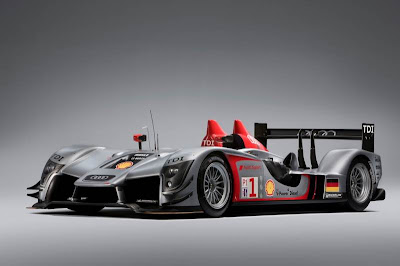
The schedule at Le Castellet
Friday, April 9
12:40–13:40 hrs free practice 1
16:10–17:10 hrs free practice 2
Saturday, April 10
09:45–10:45 hrs free practice 3
13:40–14:00 hrs qualifying (GT vehicles)
14:10–14:30 hrs qualifying (prototypes)
Sunday, April 11
08:20–08:40 hrs warm-up
11:00–19:00 hrs race
Apr 2, 2010
CODA Automotive Battery Joint Venture Secures $394 Million of Committed Capital for Expansion
California-based electric car and battery company CODA Automotive announced today that together with its joint venture partner, Lishen Power Battery, it has secured $394 million of committed capital. Lishen is one of the world’s largest manufacturers of lithium ion cells and a key battery supplier to industry leading companies such as Apple, Motorola, Samsung and Vodafone. The capital will enable the company to rapidly industrialize the all-electric CODA car’s power system for commercial volume production and support its ability to mass manufacture transportation and utility power storage battery systems.
The joint venture has secured $100 million in committed equity capital and has received a commitment for a $294 million line of credit from the Bank of Tianjin Joint-Stock Co., Ltd.
“This capital strengthens the strategic position of our joint venture and allows us to meet the rising global demand for automotive-grade lithium-ion battery and utility power storage systems,” said Kevin Czinger, President and CEO, CODA Automotive. “The U.S. and China face tremendous security and environmental challenges that we intend to address by combining our complementary capabilities and skills. This joint venture will accelerate the adoption of new energy technology while creating jobs in the U.S. and abroad.”
CODA Automotive is slated to begin deliveries of its zero tailpipe emissions, all-electric car in the fourth quarter of this year. The company is headquartered in Santa Monica, California and anticipates that it can deliver more than 14,000 vehicles to customers in California by the end of 2011. To date, CODA has raised in excess of $100 million in capital. Through its joint venture, CODA Automotive plans to establish battery manufacturing capacity in the U.S.
The joint venture has secured $100 million in committed equity capital and has received a commitment for a $294 million line of credit from the Bank of Tianjin Joint-Stock Co., Ltd.
“This capital strengthens the strategic position of our joint venture and allows us to meet the rising global demand for automotive-grade lithium-ion battery and utility power storage systems,” said Kevin Czinger, President and CEO, CODA Automotive. “The U.S. and China face tremendous security and environmental challenges that we intend to address by combining our complementary capabilities and skills. This joint venture will accelerate the adoption of new energy technology while creating jobs in the U.S. and abroad.”
CODA Automotive is slated to begin deliveries of its zero tailpipe emissions, all-electric car in the fourth quarter of this year. The company is headquartered in Santa Monica, California and anticipates that it can deliver more than 14,000 vehicles to customers in California by the end of 2011. To date, CODA has raised in excess of $100 million in capital. Through its joint venture, CODA Automotive plans to establish battery manufacturing capacity in the U.S.
Mar 28, 2010
Daimler Buses North America Hands Over Last Hybrid Bus from Order for New York City Transit
Contract for delivery of 1,350 Orion hybrid transit buses to New York City Transit (NYCT) is signed
Nearly the entire NYCT vehicle fleet consists of diesel-electric hybrid buses from Daimler Buses North America (DBNA)
Richard Ferguson, President and CEO of DBNA: “Our Orion hybrid buses have reduced fuel consumption by 5 million gallons and CO2 emissions by about 50,000 tons.”
Oriskany, U.S. – Daimler Buses North America (DBNA) has delivered the last batch of buses to New York City Transit (NYCT) from an order for a total of 1,350 Orion diesel-electric hybrid transit buses. NYCT, the largest public transport operator in the U.S., moves some seven million passengers each day.
The company currently operates a fleet of 1,679 hybrid buses, of which 1,675 are Orion VII diesel-electric hybrids from DBNA. This gives NYCT the world’s largest fleet of hybrid vehicles for local public transportation.
“This order represents the largest hybrid bus order in the history of our company,” says Richard Ferguson, President and CEO of DBNA. “Together with New York City Transit, we pioneered the hybrid bus and have proven it to be a viable option for city transit. We hope to continue this partnership with New York City Transit long into the future.”
Orion began developing and producing hybrid buses in the mid-1990s and formed a partnership with NYCT to help test the buses during their development phase. DBNA then delivered its first Orion diesel-electric hybrid bus to New York City in 1998. Although the Orion hybrid bus is used all across North America, New York City has the most units in operation.
Daimler Buses is the world’s largest manufacturer of diesel-electric hybrid buses, with over 3,000 units either in service or on order. In addition to New York, Orion hybrid buses have proven themselves in cities such as San Francisco, Houston, Toronto, and Ottawa.
“These buses have together logged nearly 100 million miles of passenger service while transporting half a billion passengers,” says Ferguson. “Their operation has reduced fuel consumption by 5 million gallons and CO2 emissions by about 50,000 tons.”
DBNA began series production of the Orion VII hybrid bus in early 2000, and Daimler Buses has since grown to become the global market leader for hybrid buses. Orion’s history of innovation continued with the introduction of lithium-ion energy storage technology for series-production buses in 2008. The new development reduced the weight of the brand’s buses, thereby further improving fuel economy. DBNA is currently further enhancing the Orion hybrid bus, and refinements are to be introduced this year.
At the heart of Orion’s diesel-electric hybrid buses is the brand’s HybriDrive system, which is manufactured by BAE Systems of Johnson City, NY. The system powers the bus with a 6.7-liter diesel engine, a generator, an electric motor, and a lithium-ion energy storage unit. The components are arranged in series and were configured especially for the Orion VII hybrid bus. The diesel engine is optimized to run at relatively constant speeds. Acceleration and deceleration are accomplished by varying the speed of the electric motor rather than the diesel engine. This results in maximum efficiency, fuel savings, and clean operation
Nearly the entire NYCT vehicle fleet consists of diesel-electric hybrid buses from Daimler Buses North America (DBNA)
Richard Ferguson, President and CEO of DBNA: “Our Orion hybrid buses have reduced fuel consumption by 5 million gallons and CO2 emissions by about 50,000 tons.”
Oriskany, U.S. – Daimler Buses North America (DBNA) has delivered the last batch of buses to New York City Transit (NYCT) from an order for a total of 1,350 Orion diesel-electric hybrid transit buses. NYCT, the largest public transport operator in the U.S., moves some seven million passengers each day.
The company currently operates a fleet of 1,679 hybrid buses, of which 1,675 are Orion VII diesel-electric hybrids from DBNA. This gives NYCT the world’s largest fleet of hybrid vehicles for local public transportation.
“This order represents the largest hybrid bus order in the history of our company,” says Richard Ferguson, President and CEO of DBNA. “Together with New York City Transit, we pioneered the hybrid bus and have proven it to be a viable option for city transit. We hope to continue this partnership with New York City Transit long into the future.”
Orion began developing and producing hybrid buses in the mid-1990s and formed a partnership with NYCT to help test the buses during their development phase. DBNA then delivered its first Orion diesel-electric hybrid bus to New York City in 1998. Although the Orion hybrid bus is used all across North America, New York City has the most units in operation.
Daimler Buses is the world’s largest manufacturer of diesel-electric hybrid buses, with over 3,000 units either in service or on order. In addition to New York, Orion hybrid buses have proven themselves in cities such as San Francisco, Houston, Toronto, and Ottawa.
“These buses have together logged nearly 100 million miles of passenger service while transporting half a billion passengers,” says Ferguson. “Their operation has reduced fuel consumption by 5 million gallons and CO2 emissions by about 50,000 tons.”
DBNA began series production of the Orion VII hybrid bus in early 2000, and Daimler Buses has since grown to become the global market leader for hybrid buses. Orion’s history of innovation continued with the introduction of lithium-ion energy storage technology for series-production buses in 2008. The new development reduced the weight of the brand’s buses, thereby further improving fuel economy. DBNA is currently further enhancing the Orion hybrid bus, and refinements are to be introduced this year.
At the heart of Orion’s diesel-electric hybrid buses is the brand’s HybriDrive system, which is manufactured by BAE Systems of Johnson City, NY. The system powers the bus with a 6.7-liter diesel engine, a generator, an electric motor, and a lithium-ion energy storage unit. The components are arranged in series and were configured especially for the Orion VII hybrid bus. The diesel engine is optimized to run at relatively constant speeds. Acceleration and deceleration are accomplished by varying the speed of the electric motor rather than the diesel engine. This results in maximum efficiency, fuel savings, and clean operation
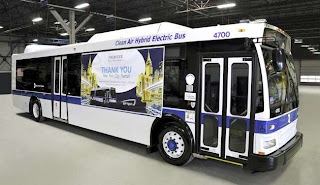
Mar 21, 2010
FORD TRANSIT CONNECT BUILDS ON ENERGY COMPANY'S SUSTAINABILITY EFFORTS
DTE Energy, a company that provides natural gas and electric utility services to 3.4 million Michigan homes and businesses, recently purchased 19 Ford Transit Connects and is exploring ways to integrate the new compact van into its vehicle fleet.
"What interested our team in the Ford Transit Connect was the fuel economy," said Gerard Huvaere, DTE Energy Fleet Operations. "It provides better fuel economy than many of the full-size pickup trucks and vans we have in our fleet."
According to Huvaere, the initial 19 Transit Connects are being used internally to transport materials from warehouses to various locations, to deliver interoffice mail and to move electric meters throughout the system. Some also are being used by the company's facilities maintenance personnel.
In addition to supporting the company's sustainability efforts, the Transit Connects help reduce operating costs, says Huvaere.
"The Transit Connect allows us to save upfront capital costs, and the fuel savings is tremendous," he said. "The trucks we replaced were older, and they were only getting 9 to 10 miles per gallon. We are achieving double that gas mileage with the Transit Connect."
Powered by a 2.0-liter I-4 engine with a four-speed automatic overdrive transmission, the Transit Connect delivers an EPA-estimated 22 mpg city and 25 mpg highway.
But fuel economy is not the only added benefit, says Huvaere.
"Many of the people who do our internal repairs take the vehicles home, so it's actually safer to keep all of their tools and equipment locked up in the Transit Connect instead of exposed in the bed of a pickup truck," he said.
According to Huvaere, DTE Energy personnel who have had an opportunity to drive the Transit Connect also like the extra headroom, the ability to access the vehicle from both the driver's and passenger's side, and the extra height in the cargo area. The front-wheel-drive Transit Connect also performs better in the Michigan snow, compared to the rear-wheel-drive pickup trucks.
Huvaere says DTE Energy is considering replacing some of the minivans currently being used by repair technicians who service homes and businesses with Transit Connects.
"The Transit Connect has more room, the same cargo capacity and costs less money to operate," he said. "And our employees really like the way it drives and handles."
Awards and accolades for the 2010 Ford Transit Connect:
* 2010 North American Truck of the Year
* 2010 Editors Choice for Vans by CAR and DRIVER magazine
* Detroit Free Press 2010 Truck of the Year
* The Detroit News 2010 Truck of the Year
* 2010 Popular Mechanics Automotive Excellence Award for Best Workhorse Vehicle
* A Great Car for the Small Business Delivery/Utility Worker by Kelley Blue Book kbb.com.
* Heavy Duty Trucking's Top 20 Product
"What interested our team in the Ford Transit Connect was the fuel economy," said Gerard Huvaere, DTE Energy Fleet Operations. "It provides better fuel economy than many of the full-size pickup trucks and vans we have in our fleet."
According to Huvaere, the initial 19 Transit Connects are being used internally to transport materials from warehouses to various locations, to deliver interoffice mail and to move electric meters throughout the system. Some also are being used by the company's facilities maintenance personnel.
In addition to supporting the company's sustainability efforts, the Transit Connects help reduce operating costs, says Huvaere.
"The Transit Connect allows us to save upfront capital costs, and the fuel savings is tremendous," he said. "The trucks we replaced were older, and they were only getting 9 to 10 miles per gallon. We are achieving double that gas mileage with the Transit Connect."
Powered by a 2.0-liter I-4 engine with a four-speed automatic overdrive transmission, the Transit Connect delivers an EPA-estimated 22 mpg city and 25 mpg highway.
But fuel economy is not the only added benefit, says Huvaere.
"Many of the people who do our internal repairs take the vehicles home, so it's actually safer to keep all of their tools and equipment locked up in the Transit Connect instead of exposed in the bed of a pickup truck," he said.
According to Huvaere, DTE Energy personnel who have had an opportunity to drive the Transit Connect also like the extra headroom, the ability to access the vehicle from both the driver's and passenger's side, and the extra height in the cargo area. The front-wheel-drive Transit Connect also performs better in the Michigan snow, compared to the rear-wheel-drive pickup trucks.
Huvaere says DTE Energy is considering replacing some of the minivans currently being used by repair technicians who service homes and businesses with Transit Connects.
"The Transit Connect has more room, the same cargo capacity and costs less money to operate," he said. "And our employees really like the way it drives and handles."
Awards and accolades for the 2010 Ford Transit Connect:
* 2010 North American Truck of the Year
* 2010 Editors Choice for Vans by CAR and DRIVER magazine
* Detroit Free Press 2010 Truck of the Year
* The Detroit News 2010 Truck of the Year
* 2010 Popular Mechanics Automotive Excellence Award for Best Workhorse Vehicle
* A Great Car for the Small Business Delivery/Utility Worker by Kelley Blue Book kbb.com.
* Heavy Duty Trucking's Top 20 Product
Chrysler Group LLC Celebrates Production Launch of Pentastar V-6 Engine at All-new Trenton, Mich., Facility
With Michigan Governor Jennifer M. Granholm and other local officials in attendance, Chrysler Group LLC celebrated the launch of its all-new Pentastar V-6 engine at an event today at the Trenton (Mich.) South Engine Plant (TSEP).
In addition to the Governor, Wayne County Executive Robert Ficano, Trenton Mayor Gerald Brown, UAW Chrysler Department Assistant Director Tim Bressler and other local officials joined Chrysler Group executives and Trenton South employees in recognizing the importance of the plant and the new engine in the future success of the Company.
"The Pentastar engine is a cornerstone of Chrysler's efforts to re-invent its business model with strong, brand-focused, world-class quality products," said Scott Garberding, Head of Manufacturing, Chrysler Group LLC. "The new Trenton South plant demonstrates the Chrysler Group's commitment to supporting economic development in Michigan. It also acknowledges the support of the International UAW and our outstanding workforce for helping us create an engine plant that can compete with the best in the world. Their efforts will help establish Trenton South as a premier manufacturer of fuel-efficient engines in support of the Company's future growth."
Chrysler Group's all-new flex-fuel Pentastar V-6 is the most advanced V-6 engine in the company's history. This new line of V-6 engines will contribute to an overall fuel-efficiency improvement of more than 25 percent across the Chrysler, Ram Truck, Jeep® and Dodge product lineup. More refined and fuel-efficient, the Pentastar engine will ultimately replace seven current Chrysler Group V-6 engines and utilize advanced technologies from the Fiat alliance such as Multiair, direct-injection and turbocharging.
The first application of this engine will be in the all-new 2011 Jeep Grand Cherokee, due out in the second quarter this year.
The start of production at Trenton South represents one piece of the Chrysler Group's revamped powertrain strategy. In December 2009, the Company announced that it would invest $179 million in its Global Engine Manufacturing Alliance (GEMA) plant in Dundee, Mich., to produce the 1.4-liter, 16-valve Fully Integrated Robotized Engine (FIRE). Together, these two plants - with a combined investment of nearly $1 billion - position Michigan at the center of Chrysler Group's powertrain offensive.
"With the start of production here in Trenton and the recently announced investment in Dundee, Chrysler Group has helped affirm Michigan's position as the world's leader in automotive innovation and excellence," said Gov. Granholm. "These projects further demonstrate that Michigan has the competitive business climate, infrastructure and talented workforce to compete in the global marketplace."
Chrysler Group announced a $730 million investment in the Pentastar program when it broke ground on the all-new 822,000-square-foot facility in May 2007. The plant will have an annual manufacturing capacity of more than 400,000 engines.
"Three years ago, Chrysler Group demonstrated its confidence in its workforce by investing in its powertrain operations," said the UAW's Bressler. "Today, the UAW members at Trenton are excited to participate in building the next generation of high quality, fuel-efficient engines for Chrysler's great lineup of vehicles and thereby, ensuring the Company's future success."
In addition to the Governor, Wayne County Executive Robert Ficano, Trenton Mayor Gerald Brown, UAW Chrysler Department Assistant Director Tim Bressler and other local officials joined Chrysler Group executives and Trenton South employees in recognizing the importance of the plant and the new engine in the future success of the Company.
"The Pentastar engine is a cornerstone of Chrysler's efforts to re-invent its business model with strong, brand-focused, world-class quality products," said Scott Garberding, Head of Manufacturing, Chrysler Group LLC. "The new Trenton South plant demonstrates the Chrysler Group's commitment to supporting economic development in Michigan. It also acknowledges the support of the International UAW and our outstanding workforce for helping us create an engine plant that can compete with the best in the world. Their efforts will help establish Trenton South as a premier manufacturer of fuel-efficient engines in support of the Company's future growth."
Chrysler Group's all-new flex-fuel Pentastar V-6 is the most advanced V-6 engine in the company's history. This new line of V-6 engines will contribute to an overall fuel-efficiency improvement of more than 25 percent across the Chrysler, Ram Truck, Jeep® and Dodge product lineup. More refined and fuel-efficient, the Pentastar engine will ultimately replace seven current Chrysler Group V-6 engines and utilize advanced technologies from the Fiat alliance such as Multiair, direct-injection and turbocharging.
The first application of this engine will be in the all-new 2011 Jeep Grand Cherokee, due out in the second quarter this year.
The start of production at Trenton South represents one piece of the Chrysler Group's revamped powertrain strategy. In December 2009, the Company announced that it would invest $179 million in its Global Engine Manufacturing Alliance (GEMA) plant in Dundee, Mich., to produce the 1.4-liter, 16-valve Fully Integrated Robotized Engine (FIRE). Together, these two plants - with a combined investment of nearly $1 billion - position Michigan at the center of Chrysler Group's powertrain offensive.
"With the start of production here in Trenton and the recently announced investment in Dundee, Chrysler Group has helped affirm Michigan's position as the world's leader in automotive innovation and excellence," said Gov. Granholm. "These projects further demonstrate that Michigan has the competitive business climate, infrastructure and talented workforce to compete in the global marketplace."
Chrysler Group announced a $730 million investment in the Pentastar program when it broke ground on the all-new 822,000-square-foot facility in May 2007. The plant will have an annual manufacturing capacity of more than 400,000 engines.
"Three years ago, Chrysler Group demonstrated its confidence in its workforce by investing in its powertrain operations," said the UAW's Bressler. "Today, the UAW members at Trenton are excited to participate in building the next generation of high quality, fuel-efficient engines for Chrysler's great lineup of vehicles and thereby, ensuring the Company's future success."
Mar 14, 2010
Freightliner Custom Chassis Corporation's All-Electric Walk-In Van Chassis Debuts at NTEA Work Truck Show
Freightliner Custom Chassis Corporation (FCCC) continues its legacy of engineering alternative-power products for the commercial vehicle industry with the introduction of its highly anticipated plug-in all-electric walk-in van (WIV) chassis. The new chassis model is the only one domestically engineered and the first in the industry to be completely all-electric (includes HVAC system) in North America.
The all-electric chassis, developed in partnership with Enova Systems (NYSE:ENA and AIM:ENV and ENVS), a leading developer and producer of electric and hybrid-electric drive system technologies for commercial vehicle OEMs, is built on the popular FCCC MT-45 WIV chassis platform.
FCCC presented the preproduction all-electric WIV chassis model at the 2010 National Truck Equipment Association (NTEA) Work Truck Show (Booth #3035).
"In partnership with Enova we have developed an all-electric chassis to meet the environmental, economic and performance needs of our commercial vehicle customers," said Bob Harbin, FCCC president. "Our vision is clearly focused on transitioning the all-electric chassis into the mainstream of our walk-in van production programs. This new program demonstrates that FCCC remains fully committed to engineering chassis options that lower operating costs and decrease carbon footprints for our customers.
"Unlike competitive models, our all-electric chassis is custom-built from the ground up for the walk-in van market, integrating the proven ergonomic advantages of WIV bodies," Harbin added. "Competitor chassis are a cab chassis configuration and end up as box trucks typically built for the trucking industry. Competitor products do not offer the ergonomic benefits and safety features of a WIV such as curb-side exit, walk-through cargo area, direct access to cargo area from driver's station, etc."
Addressing the discussion in the industry surrounding recent federal funding for all-electric technology, Jonathan Randall, sales and marketing director at FCCC added, "FCCC initiated our all-electric project well before stimulus money and federal grants were available for alternative-power transportation projects. FCCC viewed the all-electric project as the logical next step in its alternative-power product offerings, as well as a strategic opportunity to continue its leadership role in the WIV industry."
Zero Tailpipe Emissions Without Sacrificing Performance
The new all-electric chassis enables fleet operators to virtually eliminate harmful emissions and cut operating and maintenance costs while delivering the performance and driver comfort features FCCC customers have come to expect. On select delivery and service routes, studies show that customers will save up to $15,000 per vehicle annually compared with traditionally powered walk-in vans. The quiet operation of the all-electric chassis also makes for an enjoyable driver experience. This new chassis has a flat-leaf spring front and rear suspension, allowing for a smooth, solid ride that minimizes cargo shifts on uneven road surfaces.
The development program with Enova involved the engineering and integration of Enova's 120kW all-electric drive system technology into the new MT-45 chassis. Ideal for the pickup and delivery market, the MT-45 chassis boasts a GVWR of 14,000 to 19,500 lbs. The durable steel straight-rail chassis frame reduces flex and bowing to minimize chassis stress while carrying heavy payloads.
"Collaborating with Freightliner Custom Chassis Corporation has enabled us to achieve our shared goal of introducing all-electric drive technology into the walk-in van market," said Mike Staran, president and CEO of Enova Systems. "The FCCC-Enova partnership is accelerating the broad deployment of EV technology in this critical vehicle segment while improving the environment and helping to reduce U.S. dependence on imported energy."
Powered by Tesla Motors lithium ion batteries, the chassis is 100 percent electric, including its HVAC system, making it the only fully featured WIV chassis in the industry to be completely electrically powered. FCCC is the first company within the industry to utilize Tesla batteries for commercial applications.
The all-electric drive system features battery packs that provides an up to 100-mile driving range on a single charge, making it ideal for pickup and delivery applications. The battery pack will charge from fully depleted to fully charged in six to eight hours.
The batteries featured on the electric system also capture and store energy during the regenerative braking phase of the vehicle's operation. The regenerative braking system reduces friction during braking, resulting in less brake wear and extended brake life. The regenerative braking system saves energy by recycling and storing it, which can then be reused to propel the vehicle instead of losing it to heat, as is the case with traditional brakes.
Other features include a parking pawl within the gear box and a push-button shifter for improved efficiency.
The all-electric MT-45 chassis is expected to go into full production during the first quarter of 2011 and will undergo testing with major U.S. pickup and delivery fleets.
Green Technology Legacy
FCCC and its parent company, Daimler Trucks North America LLC (DTNA), maintain a legacy of providing innovative technologies that benefit customers and the environment. FCCC's commitment to green technologies is in line with Daimler AG's global initiative called, "Shaping Future Transportation." Launched in Stuttgart, Germany, by Daimler in 2007, the initiative is focused on reducing category emissions pollutants, carbon dioxide and fuel consumption.
In August 2008, Daimler announced the opening of the Global Hybrid Center at Mitsubishi Fuso Truck and Bus Corporation in Kawasaki, Japan. The center is the worldwide hub for Daimler's hybrid development.
"FCCC is proud to continue to play an important role in Daimler's global initiative," said Randall. "We are committed to developing new chassis that offer a superior level of comfort, reliability, performance and durability that our customers need from their vehicles, while also manufacturing products that are environmentally responsible."
Along with the all-electric chassis, FCCC has extensive experience manufacturing compressed natural gas (CNG) WIV chassis, currently manufactures hybrid-electric vehicle (HEV) chassis and will offer full production of the hydraulic hybrid vehicle (HHV) chassis in Q4 2010 for the walk-in van market segment. These alternative-power vehicles have proven to offer significant fuel savings benefits.
FCCC also designs and manufactures alternative-fuel chassis for the commercial bus and motorhome market segments. In 2008, FCCC introduced ecoFRED™, the motorhome industry's first hybrid-electric chassis, and the FCCC MB-HEV hybrid-electric commercial bus chassis in response to a growing customer demand for alternative-fuel power that provides the same excellent performance and durability as FCCC's premium diesel-powered chassis. At the 2009 NTEA Work Truck Show, FCCC introduced its HHV chassis to the commercial vehicle industry.
For more information about the new plug-in all-electric chassis or any of the FCCC WIV chassis, please visit www.freightlinerchassis.com.
Enova Systems (NYSE:ENA and AIM:ENV and ENVS) is a leading supplier of efficient, environmentally friendly digital power components and systems products. The Company's core competencies are focused on the development and commercialization of power management and conversion systems for mobile applications. Enova applies unique "enabling technologies" in the areas of alternative energy propulsion systems for light and heavy-duty vehicles as well as power conditioning and management systems for distributed generation systems. The Company develops, designs and produces non-invasive drive systems and related components for electric, hybrid-electric, and fuel cell powered vehicles in both the "new" and "retrofit" vehicle sales market. For further information, contact Enova Systems directly, or visit www.enovasystems.com.
Freightliner Custom Chassis Corporation manufactures premium chassis for the motorhome, delivery walk-in van, and school bus and shuttle bus markets. Freightliner Custom Chassis Corporation is a subsidiary of Daimler Trucks North America LLC, a Daimler company.
The all-electric chassis, developed in partnership with Enova Systems (NYSE:ENA and AIM:ENV and ENVS), a leading developer and producer of electric and hybrid-electric drive system technologies for commercial vehicle OEMs, is built on the popular FCCC MT-45 WIV chassis platform.
FCCC presented the preproduction all-electric WIV chassis model at the 2010 National Truck Equipment Association (NTEA) Work Truck Show (Booth #3035).
"In partnership with Enova we have developed an all-electric chassis to meet the environmental, economic and performance needs of our commercial vehicle customers," said Bob Harbin, FCCC president. "Our vision is clearly focused on transitioning the all-electric chassis into the mainstream of our walk-in van production programs. This new program demonstrates that FCCC remains fully committed to engineering chassis options that lower operating costs and decrease carbon footprints for our customers.
"Unlike competitive models, our all-electric chassis is custom-built from the ground up for the walk-in van market, integrating the proven ergonomic advantages of WIV bodies," Harbin added. "Competitor chassis are a cab chassis configuration and end up as box trucks typically built for the trucking industry. Competitor products do not offer the ergonomic benefits and safety features of a WIV such as curb-side exit, walk-through cargo area, direct access to cargo area from driver's station, etc."
Addressing the discussion in the industry surrounding recent federal funding for all-electric technology, Jonathan Randall, sales and marketing director at FCCC added, "FCCC initiated our all-electric project well before stimulus money and federal grants were available for alternative-power transportation projects. FCCC viewed the all-electric project as the logical next step in its alternative-power product offerings, as well as a strategic opportunity to continue its leadership role in the WIV industry."
Zero Tailpipe Emissions Without Sacrificing Performance
The new all-electric chassis enables fleet operators to virtually eliminate harmful emissions and cut operating and maintenance costs while delivering the performance and driver comfort features FCCC customers have come to expect. On select delivery and service routes, studies show that customers will save up to $15,000 per vehicle annually compared with traditionally powered walk-in vans. The quiet operation of the all-electric chassis also makes for an enjoyable driver experience. This new chassis has a flat-leaf spring front and rear suspension, allowing for a smooth, solid ride that minimizes cargo shifts on uneven road surfaces.
The development program with Enova involved the engineering and integration of Enova's 120kW all-electric drive system technology into the new MT-45 chassis. Ideal for the pickup and delivery market, the MT-45 chassis boasts a GVWR of 14,000 to 19,500 lbs. The durable steel straight-rail chassis frame reduces flex and bowing to minimize chassis stress while carrying heavy payloads.
"Collaborating with Freightliner Custom Chassis Corporation has enabled us to achieve our shared goal of introducing all-electric drive technology into the walk-in van market," said Mike Staran, president and CEO of Enova Systems. "The FCCC-Enova partnership is accelerating the broad deployment of EV technology in this critical vehicle segment while improving the environment and helping to reduce U.S. dependence on imported energy."
Powered by Tesla Motors lithium ion batteries, the chassis is 100 percent electric, including its HVAC system, making it the only fully featured WIV chassis in the industry to be completely electrically powered. FCCC is the first company within the industry to utilize Tesla batteries for commercial applications.
The all-electric drive system features battery packs that provides an up to 100-mile driving range on a single charge, making it ideal for pickup and delivery applications. The battery pack will charge from fully depleted to fully charged in six to eight hours.
The batteries featured on the electric system also capture and store energy during the regenerative braking phase of the vehicle's operation. The regenerative braking system reduces friction during braking, resulting in less brake wear and extended brake life. The regenerative braking system saves energy by recycling and storing it, which can then be reused to propel the vehicle instead of losing it to heat, as is the case with traditional brakes.
Other features include a parking pawl within the gear box and a push-button shifter for improved efficiency.
The all-electric MT-45 chassis is expected to go into full production during the first quarter of 2011 and will undergo testing with major U.S. pickup and delivery fleets.
Green Technology Legacy
FCCC and its parent company, Daimler Trucks North America LLC (DTNA), maintain a legacy of providing innovative technologies that benefit customers and the environment. FCCC's commitment to green technologies is in line with Daimler AG's global initiative called, "Shaping Future Transportation." Launched in Stuttgart, Germany, by Daimler in 2007, the initiative is focused on reducing category emissions pollutants, carbon dioxide and fuel consumption.
In August 2008, Daimler announced the opening of the Global Hybrid Center at Mitsubishi Fuso Truck and Bus Corporation in Kawasaki, Japan. The center is the worldwide hub for Daimler's hybrid development.
"FCCC is proud to continue to play an important role in Daimler's global initiative," said Randall. "We are committed to developing new chassis that offer a superior level of comfort, reliability, performance and durability that our customers need from their vehicles, while also manufacturing products that are environmentally responsible."
Along with the all-electric chassis, FCCC has extensive experience manufacturing compressed natural gas (CNG) WIV chassis, currently manufactures hybrid-electric vehicle (HEV) chassis and will offer full production of the hydraulic hybrid vehicle (HHV) chassis in Q4 2010 for the walk-in van market segment. These alternative-power vehicles have proven to offer significant fuel savings benefits.
FCCC also designs and manufactures alternative-fuel chassis for the commercial bus and motorhome market segments. In 2008, FCCC introduced ecoFRED™, the motorhome industry's first hybrid-electric chassis, and the FCCC MB-HEV hybrid-electric commercial bus chassis in response to a growing customer demand for alternative-fuel power that provides the same excellent performance and durability as FCCC's premium diesel-powered chassis. At the 2009 NTEA Work Truck Show, FCCC introduced its HHV chassis to the commercial vehicle industry.
For more information about the new plug-in all-electric chassis or any of the FCCC WIV chassis, please visit www.freightlinerchassis.com.
Enova Systems (NYSE:ENA and AIM:ENV and ENVS) is a leading supplier of efficient, environmentally friendly digital power components and systems products. The Company's core competencies are focused on the development and commercialization of power management and conversion systems for mobile applications. Enova applies unique "enabling technologies" in the areas of alternative energy propulsion systems for light and heavy-duty vehicles as well as power conditioning and management systems for distributed generation systems. The Company develops, designs and produces non-invasive drive systems and related components for electric, hybrid-electric, and fuel cell powered vehicles in both the "new" and "retrofit" vehicle sales market. For further information, contact Enova Systems directly, or visit www.enovasystems.com.
Freightliner Custom Chassis Corporation manufactures premium chassis for the motorhome, delivery walk-in van, and school bus and shuttle bus markets. Freightliner Custom Chassis Corporation is a subsidiary of Daimler Trucks North America LLC, a Daimler company.
Mar 11, 2010
Smith Electric Vehicles U.S. Makes Offer to Buy Smith Electric Vehicles U.K. from Tanfield Group
Smith Electric Vehicles U.S. Corporation ("Smith U.S.") announced today that it has made a conditional offer to buy the Smith Electric Vehicles business based in the U.K. ("Smith UK Division") from Tanfield Group Plc. ("Tanfield"). The offer is conditional upon successful financing by Smith U.S. and shareholder approvals on the part of Tanfield. The board of Tanfield has granted Smith U.S. a four month period of exclusivity.
In connection with the purchase of the Smith UK Division, the transaction includes the purchase of all of the Smith U.S. common stock currently held by Tanfield, as well as the License Agreement by and between Tanfield and Smith U.S., and the intellectual property necessary to allow the combined businesses to operate globally. Smith U.S. has retained Jefferies & Company, Inc. as its advisor on the transaction.
"Once completed, this transaction will create a unified entity that will be well positioned globally for growth in the rapidly expanding electric commercial vehicle market," said Bryan Hansel, CEO of Smith U.S. "We believe this combination will create operational efficiencies and market synergies that will help Smith continue its strong sales momentum and cost reductions."
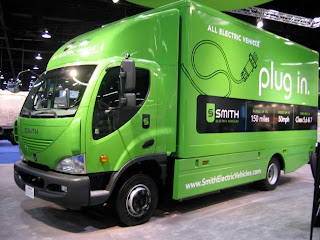
Smith U.S., headquartered in Kansas City, Missouri, is a privately held company owned by private investors, senior management and Tanfield. Tanfield is the parent company of the Smith U.K. Division, a leading manufacturer of zero-emissions battery-electric commercial vehicles in Europe since the 1920s.
In connection with the purchase of the Smith UK Division, the transaction includes the purchase of all of the Smith U.S. common stock currently held by Tanfield, as well as the License Agreement by and between Tanfield and Smith U.S., and the intellectual property necessary to allow the combined businesses to operate globally. Smith U.S. has retained Jefferies & Company, Inc. as its advisor on the transaction.
"Once completed, this transaction will create a unified entity that will be well positioned globally for growth in the rapidly expanding electric commercial vehicle market," said Bryan Hansel, CEO of Smith U.S. "We believe this combination will create operational efficiencies and market synergies that will help Smith continue its strong sales momentum and cost reductions."
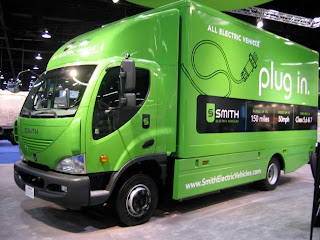
Smith U.S., headquartered in Kansas City, Missouri, is a privately held company owned by private investors, senior management and Tanfield. Tanfield is the parent company of the Smith U.K. Division, a leading manufacturer of zero-emissions battery-electric commercial vehicles in Europe since the 1920s.
2011 FORD F-SERIES SUPER DUTY POWER STROKE DIESEL IS CLEANEST EVER; FUEL ECONOMY GREATLY IMPROVED
The all-new 2011 Ford F-Series Super Duty delivers best-in-class torque, horsepower, towing and payload capability – and does it all more efficiently, resulting in less fuel usage and extended maintenance intervals that can translate directly into bottom-line savings for customers.
"The 2011 Super Duty is not only the most powerful, most capable and fuel-efficient heavy-duty pickup truck on the road, it performs the tough jobs with even more efficiency than ever before," said Doug Scott, truck group marketing manager. "Customers can be confident that Super Duty's class-leading capability comes with Ford's 'and solution' of best-in-class fuel economy."
All-new diesel and gas engine powertrains are the backbone of the 2011 Super Duty's best-in-class towing (26,400 pounds for F-550 chassis cab with fifth-wheel hitch) and payload capability (6,520 pounds for F-350 dual rear-wheel pickup). The Ford-designed, Ford-engineered and Ford-built 6.7-liter Power Stroke V-8 turbocharged diesel engine produces best-in-class 735 ft.-lb. of torque at 1,600 rpm and best-in-class 390 horsepower at 2,800 rpm. The new engine is compatible up to B20 biodiesel fuel as well.
The new 6.2-liter V-8 gasoline engine also boasts best-in-class numbers of 405 ft.-lb. of torque at 4,500 rpm and 385 horsepower at 5,500 rpm. The new engine is E85 compatible.
Mated to each engine is the all-new 6R140 heavy-duty TorqShift six-speed automatic transmission. The added feature content and overall efficiency of the transmission are the main reasons for the improved fuel economy. The all-new 2011 Ford F-Series Super Duty equipped with the 6.7-liter Power Stroke diesel averages an 18 percent improvement for pickup models and up to 25 percent improvement for chassis cabs versus 2010 models. Trucks equipped with new base 6.2-liter V-8 gas engine average a 15 percent improvement versus 2010 models.
"The new transmission is a 'clean-sheet' design, developed specifically to handle the significantly increased torque produced by the new diesel engine and the higher rotational speeds produced by the new gas engine, and to deliver the power to the wheels seamlessly and efficiently for heavy-duty truck customers," said Al Bruck, transmission engineering manager. "Each system and component was scrutinized to deliver optimum performance."
Here's a closer look at what was achieved and the benefits to the customer:
* New torque converter that locks at a far lower rpm than the competition: The new, stronger torque converter is core to the improved transmission performance. One key component is the long-travel turbine damper that allows the transmission to lock earlier, at a lower rpm, which translates to less slip and more fuel efficiency. The new transmission locks down to 900 rpm, which is about 200 rpm less than the outgoing product and more than 100 rpm less than competitors. The second key component of the torque converter is the closed-piston design. This design allows for better control of the lock-up clutch, which enables controlled converter clutch slip during lock-to-lock upshifts that are seamless to the customer.
– Customer fuel economy benefit: Locked converter operation at lower speeds means less wasted heat energy and better fuel economy.
* Optimized shift and converter lock-up schedule: After analyzing the entire shift schedule, Ford calibration engineers fine-tuned it by measuring and optimizing the fuel flow. The system recognizes light or heavy throttle use, and puts the transmission in the right gear for best performance and efficiency. The entire operating range has been optimized to get the best fuel economy by locking up the converter as soon as possible and as much as possible.
– Customer fuel economy benefit: Optimizing the shift schedule and lock schedule ensures customers automatically operate in the most efficient gears and save fuel.
* Gearing and double-overdrive: The 6R140 transmission has a ratio span of about 5.9, which is quite a bit wider than competitors. This wider span means the transmission has a deeper first gear that allows customers to get the load moving quicker, and a tall overdrive ratio for good highway efficiency. While the gearing itself is important, the key to overall efficiency is matching that gearing to the correct axle. With the diesel engine, up to four axle ratios are available on the pickups – 3.31, 3.55, 3.73 and 4.30. Matching up the gearing with the right axles means better overall efficiency.
– Customer fuel economy benefit: The double-overdrive gear means even if a customer gets a downshift on the highway, the transmission remains in overdrive. Also, the F-450 pickup went from a 4.88 axle to a 4.30 axle at launch for the 2011 model mated to the wide ratio span of the transmission. This and other optimizations mean the F-450 now has about a 30 percent improvement in fuel economy.
* Optimized pumping pressure: A certain amount of pressure is required to hold the clutches together so they don't slip. The trick is to have the right amount of pressure to do the job. Too much pressure wastes fuel. The solution is to optimize the size of the pump and precisely control the pressure for all operating conditions.
– Customer fuel economy benefit: At highway speeds, for example, the line pressure is reduced, which helps save fuel. The system maintains the right amount of pressure for any given speed range. The less energy needed for internal pump pressure means less fuel used.
* Optimized drainback to reduce spin losses: A main objective is to get the fluid through the main barrel to lubricate and cool components, and get it back to the sump as quickly as possible. This reduces windage and parasitic loss. The clutch friction plates were designed to allow fluid to flow through them efficiently for cooling and reduced drag. Clutch housings, connecting shells and the main case housing were optimized to quickly drain the fluid out of rotating components and back into the sump.
– Customer fuel economy benefit: Fewer parasitic losses due to reduced churning of fluid increases fuel economy.
* Warmer operating temperature: Tied in with spin losses, the 6R140 cooling system has been optimized to allow for the proper amount of cooling when towing heavy loads in high ambient temperatures, while running at an overall higher stabilized temperature. This higher stabilized temperature lowers the viscosity and helps the fluid flow more easily, which reduces parasitic losses and saves fuel. The fluid also warms up faster because it does not flow to the cooling circuit until properly warmed up. Faster warm-up also reduces overall parasitic losses.
– Customer fuel economy benefit: Fewer parasitic losses due to reduced fluid viscosity translates to less internal drag on the system and increases fuel economy.
Lighter, more efficient than competition
The 6R140 transmission is about 25 pounds lighter than those of competitors. The new engines are lighter than the outgoing products as well, which altogether means much more efficient power flow on a pound-for-pound basis. The 6R140 also has a 150,000-mile fluid change interval, which is 2½ times greater than the outgoing product. A patent-pending high-efficiency dual-media filter is the main reason for the extended maintenance interval, which is another savings for customers.
Cleanest Power Stroke ever
The new 6.7-liter Power Stroke V-8 turbocharged diesel employs an aftertreatment system to help comply with 2010 federal regulations to reduce NOx levels in diesel emissions by more than 80 percent compared with the previous standard. The Ford aftertreatment system is a three-stage process; a key component is the use of Diesel Exhaust Fluid (DEF).
Injection of DEF to reduce NOx is a proven technology that's been used throughout the automotive industry. Unlike other strategies used to control NOx, the DEF system allows the diesel engine to run at its optimum range in terms of fuel mixture. Some systems require the engine to run richer – which can be harmful to diesel engines – in order to control the NOx.
The aftertreatment system works like this:
Step One: Cleaning and Heating – The first step in cleaning the diesel exhaust occurs when the exhaust stream enters the Diesel Oxidation Catalyst (DOC). The role of the DOC is twofold. First, it converts and oxidizes hydrocarbons into water and carbon dioxide. This conversion happens at about 250 degrees Celsius.
Second, the DOC is used to provide and promote heat, using specific engine management strategies, into the exhaust system. Through appropriate thermal management, this heat increases the conversion efficiency of the downstream subsystems in reducing emissions.
Step Two: Knocking Out the NOx – The next step in the process is what's known as Selective Catalytic Reduction (SCR). In this process, the NOx in the exhaust stream is converted into water and inert nitrogen, which is present in the atmosphere and harmless. Before the exhaust gas enters the SCR chamber, it is dosed with DEF, an aqueous solution that is approximately 67.5 percent water and 32.5 percent pure urea.
When heated, the DEF splits into ammonia and carbon dioxide. These molecules are atomized and vaporized, then enter a mixer that resembles a corkscrew. This twist mixer evenly distributes the ammonia within the exhaust flow. The ammonia enters the SCR module, which contains a catalyzed substrate, and through chemical reactions combines and converts the NOx and ammonia into the harmless inert nitrogen and water. Dosing occurs between 200 and 500 degrees Celsius.
Step Three: Scrubbing Away the Soot – The final part of the cleansing system for the diesel exhaust gas involves the Diesel Particulate Filter (DPF). The DPF traps any remaining soot, which is then periodically burned away, known as regenerating, when sensors detect the trap is full. The regeneration process sees temperatures in excess of 600 degrees Celsius to burn away soot.
This industry-proven technology ensures that the new 6.7-liter diesel is the cleanest Power Stroke ever, as well as the most fuel-efficient.
"Having this diesel designed in-house at Ford meant we were able to work on optimizations and refinements right from the start," said Tim Ogilvie, vehicle energy supervisor. "We're able to deliver to customers a more refined, more fuel-efficient Super Duty, with class-leading torque and horsepower and the class-leading capability they demand."
"The 2011 Super Duty is not only the most powerful, most capable and fuel-efficient heavy-duty pickup truck on the road, it performs the tough jobs with even more efficiency than ever before," said Doug Scott, truck group marketing manager. "Customers can be confident that Super Duty's class-leading capability comes with Ford's 'and solution' of best-in-class fuel economy."
All-new diesel and gas engine powertrains are the backbone of the 2011 Super Duty's best-in-class towing (26,400 pounds for F-550 chassis cab with fifth-wheel hitch) and payload capability (6,520 pounds for F-350 dual rear-wheel pickup). The Ford-designed, Ford-engineered and Ford-built 6.7-liter Power Stroke V-8 turbocharged diesel engine produces best-in-class 735 ft.-lb. of torque at 1,600 rpm and best-in-class 390 horsepower at 2,800 rpm. The new engine is compatible up to B20 biodiesel fuel as well.
The new 6.2-liter V-8 gasoline engine also boasts best-in-class numbers of 405 ft.-lb. of torque at 4,500 rpm and 385 horsepower at 5,500 rpm. The new engine is E85 compatible.
Mated to each engine is the all-new 6R140 heavy-duty TorqShift six-speed automatic transmission. The added feature content and overall efficiency of the transmission are the main reasons for the improved fuel economy. The all-new 2011 Ford F-Series Super Duty equipped with the 6.7-liter Power Stroke diesel averages an 18 percent improvement for pickup models and up to 25 percent improvement for chassis cabs versus 2010 models. Trucks equipped with new base 6.2-liter V-8 gas engine average a 15 percent improvement versus 2010 models.
"The new transmission is a 'clean-sheet' design, developed specifically to handle the significantly increased torque produced by the new diesel engine and the higher rotational speeds produced by the new gas engine, and to deliver the power to the wheels seamlessly and efficiently for heavy-duty truck customers," said Al Bruck, transmission engineering manager. "Each system and component was scrutinized to deliver optimum performance."
Here's a closer look at what was achieved and the benefits to the customer:
* New torque converter that locks at a far lower rpm than the competition: The new, stronger torque converter is core to the improved transmission performance. One key component is the long-travel turbine damper that allows the transmission to lock earlier, at a lower rpm, which translates to less slip and more fuel efficiency. The new transmission locks down to 900 rpm, which is about 200 rpm less than the outgoing product and more than 100 rpm less than competitors. The second key component of the torque converter is the closed-piston design. This design allows for better control of the lock-up clutch, which enables controlled converter clutch slip during lock-to-lock upshifts that are seamless to the customer.
– Customer fuel economy benefit: Locked converter operation at lower speeds means less wasted heat energy and better fuel economy.
* Optimized shift and converter lock-up schedule: After analyzing the entire shift schedule, Ford calibration engineers fine-tuned it by measuring and optimizing the fuel flow. The system recognizes light or heavy throttle use, and puts the transmission in the right gear for best performance and efficiency. The entire operating range has been optimized to get the best fuel economy by locking up the converter as soon as possible and as much as possible.
– Customer fuel economy benefit: Optimizing the shift schedule and lock schedule ensures customers automatically operate in the most efficient gears and save fuel.
* Gearing and double-overdrive: The 6R140 transmission has a ratio span of about 5.9, which is quite a bit wider than competitors. This wider span means the transmission has a deeper first gear that allows customers to get the load moving quicker, and a tall overdrive ratio for good highway efficiency. While the gearing itself is important, the key to overall efficiency is matching that gearing to the correct axle. With the diesel engine, up to four axle ratios are available on the pickups – 3.31, 3.55, 3.73 and 4.30. Matching up the gearing with the right axles means better overall efficiency.
– Customer fuel economy benefit: The double-overdrive gear means even if a customer gets a downshift on the highway, the transmission remains in overdrive. Also, the F-450 pickup went from a 4.88 axle to a 4.30 axle at launch for the 2011 model mated to the wide ratio span of the transmission. This and other optimizations mean the F-450 now has about a 30 percent improvement in fuel economy.
* Optimized pumping pressure: A certain amount of pressure is required to hold the clutches together so they don't slip. The trick is to have the right amount of pressure to do the job. Too much pressure wastes fuel. The solution is to optimize the size of the pump and precisely control the pressure for all operating conditions.
– Customer fuel economy benefit: At highway speeds, for example, the line pressure is reduced, which helps save fuel. The system maintains the right amount of pressure for any given speed range. The less energy needed for internal pump pressure means less fuel used.
* Optimized drainback to reduce spin losses: A main objective is to get the fluid through the main barrel to lubricate and cool components, and get it back to the sump as quickly as possible. This reduces windage and parasitic loss. The clutch friction plates were designed to allow fluid to flow through them efficiently for cooling and reduced drag. Clutch housings, connecting shells and the main case housing were optimized to quickly drain the fluid out of rotating components and back into the sump.
– Customer fuel economy benefit: Fewer parasitic losses due to reduced churning of fluid increases fuel economy.
* Warmer operating temperature: Tied in with spin losses, the 6R140 cooling system has been optimized to allow for the proper amount of cooling when towing heavy loads in high ambient temperatures, while running at an overall higher stabilized temperature. This higher stabilized temperature lowers the viscosity and helps the fluid flow more easily, which reduces parasitic losses and saves fuel. The fluid also warms up faster because it does not flow to the cooling circuit until properly warmed up. Faster warm-up also reduces overall parasitic losses.
– Customer fuel economy benefit: Fewer parasitic losses due to reduced fluid viscosity translates to less internal drag on the system and increases fuel economy.
Lighter, more efficient than competition
The 6R140 transmission is about 25 pounds lighter than those of competitors. The new engines are lighter than the outgoing products as well, which altogether means much more efficient power flow on a pound-for-pound basis. The 6R140 also has a 150,000-mile fluid change interval, which is 2½ times greater than the outgoing product. A patent-pending high-efficiency dual-media filter is the main reason for the extended maintenance interval, which is another savings for customers.
Cleanest Power Stroke ever
The new 6.7-liter Power Stroke V-8 turbocharged diesel employs an aftertreatment system to help comply with 2010 federal regulations to reduce NOx levels in diesel emissions by more than 80 percent compared with the previous standard. The Ford aftertreatment system is a three-stage process; a key component is the use of Diesel Exhaust Fluid (DEF).
Injection of DEF to reduce NOx is a proven technology that's been used throughout the automotive industry. Unlike other strategies used to control NOx, the DEF system allows the diesel engine to run at its optimum range in terms of fuel mixture. Some systems require the engine to run richer – which can be harmful to diesel engines – in order to control the NOx.
The aftertreatment system works like this:
Step One: Cleaning and Heating – The first step in cleaning the diesel exhaust occurs when the exhaust stream enters the Diesel Oxidation Catalyst (DOC). The role of the DOC is twofold. First, it converts and oxidizes hydrocarbons into water and carbon dioxide. This conversion happens at about 250 degrees Celsius.
Second, the DOC is used to provide and promote heat, using specific engine management strategies, into the exhaust system. Through appropriate thermal management, this heat increases the conversion efficiency of the downstream subsystems in reducing emissions.
Step Two: Knocking Out the NOx – The next step in the process is what's known as Selective Catalytic Reduction (SCR). In this process, the NOx in the exhaust stream is converted into water and inert nitrogen, which is present in the atmosphere and harmless. Before the exhaust gas enters the SCR chamber, it is dosed with DEF, an aqueous solution that is approximately 67.5 percent water and 32.5 percent pure urea.
When heated, the DEF splits into ammonia and carbon dioxide. These molecules are atomized and vaporized, then enter a mixer that resembles a corkscrew. This twist mixer evenly distributes the ammonia within the exhaust flow. The ammonia enters the SCR module, which contains a catalyzed substrate, and through chemical reactions combines and converts the NOx and ammonia into the harmless inert nitrogen and water. Dosing occurs between 200 and 500 degrees Celsius.
Step Three: Scrubbing Away the Soot – The final part of the cleansing system for the diesel exhaust gas involves the Diesel Particulate Filter (DPF). The DPF traps any remaining soot, which is then periodically burned away, known as regenerating, when sensors detect the trap is full. The regeneration process sees temperatures in excess of 600 degrees Celsius to burn away soot.
This industry-proven technology ensures that the new 6.7-liter diesel is the cleanest Power Stroke ever, as well as the most fuel-efficient.
"Having this diesel designed in-house at Ford meant we were able to work on optimizations and refinements right from the start," said Tim Ogilvie, vehicle energy supervisor. "We're able to deliver to customers a more refined, more fuel-efficient Super Duty, with class-leading torque and horsepower and the class-leading capability they demand."
An Electric Car with a Whole New Idea
Aurica is an Electric Car with a purpose: to make electric cars more practical while saving 4700 NUMMI jobs, the Bay Area economy, and the environment - all at the same time.
NUMMI, the only auto manufacturing plant west of the Mississippi, here in Fremont, California, currently employs about 4,700 people. They are finishing the final work orders placed for the Cash-For-Clunkers Government Incentive Program that was so successful last year.
On March 31, 2010, when Toyota’s contract expires the plant will shut down. NUMMI’s workforce and families stand to lose their entire livelihoods. Not only that, Another 50,000 or more people are employed throughout the Bay Area providing this massive manufacturing plant with parts and supplies.
By making electric cars at this facility we can save all of these jobs, and save a major cornerstone of the Bay Area economy. The Aurica E-Car becomes a catalyst for new economic expansion in Northern California.
Enviromentally more advanced.
The 100% emission-free Aurica E-Car helps save the environment in more ways than one. Other electric cars use only “grid” power, which comes mainly from fossil fuels like oil and coal. The Aurica Motors concept is to recharge our interchangeable quick swap battery with solar, wind and tidal energy, storing renewable power for use even when the sun isn’t shining and the wind isn’t blowing.
Go farther.
Aurica has overcome the two largest obstacles to buying electric cars: overall driving distance and long recharging times. The Aurica E-Car goes farther on a single charge than ever possible before. Aurica’s new technologies run much more efficiently than typical motor drives. And getting a new charge can take as little as three minutes. Pull into one of our PEP (Power Exchange Package) modular charging kiosks and quickly swap out the battery with one that’s freshly charged with renewable energy. Or, for more convenience, simply plug it in at home.
Want a new ride? Swap body styles.
Because Electric Cars have so few moving parts, the Aurica frame and drive system could easily last for 20 years or more with minimal maintenance. Instead of buying a new car every 2 to 5 years, you can just swap out an older body style for a brand new look for less than a third the price of a new car. Now that’s economical sustainability.
The Aurica E-Car Series will begin with four body styles all built to fit on the same standard chassis. You can get a sporty economy car, a mid-sized 4-door sedan, a stylish SUV hatchback, or a light pickup truck. More body styles and color combinations will be available every year. We will even assist custom body designers to offer more exotic designs that fit the chassis perfectly.
The best of everything.
The beauty of Aurica Motors electric car design is that you can make them with existing off-the-shelf car parts. This common supply base already exists. Someone just has to pull it all together. That’s what Aurica Motors is doing. We are sourcing and testing the best of the industry and adding our own innovations to create an electric car that does more for the people, the economy, and the environment than ever before.
NUMMI, the only auto manufacturing plant west of the Mississippi, here in Fremont, California, currently employs about 4,700 people. They are finishing the final work orders placed for the Cash-For-Clunkers Government Incentive Program that was so successful last year.
On March 31, 2010, when Toyota’s contract expires the plant will shut down. NUMMI’s workforce and families stand to lose their entire livelihoods. Not only that, Another 50,000 or more people are employed throughout the Bay Area providing this massive manufacturing plant with parts and supplies.
By making electric cars at this facility we can save all of these jobs, and save a major cornerstone of the Bay Area economy. The Aurica E-Car becomes a catalyst for new economic expansion in Northern California.
Enviromentally more advanced.
The 100% emission-free Aurica E-Car helps save the environment in more ways than one. Other electric cars use only “grid” power, which comes mainly from fossil fuels like oil and coal. The Aurica Motors concept is to recharge our interchangeable quick swap battery with solar, wind and tidal energy, storing renewable power for use even when the sun isn’t shining and the wind isn’t blowing.
Go farther.
Aurica has overcome the two largest obstacles to buying electric cars: overall driving distance and long recharging times. The Aurica E-Car goes farther on a single charge than ever possible before. Aurica’s new technologies run much more efficiently than typical motor drives. And getting a new charge can take as little as three minutes. Pull into one of our PEP (Power Exchange Package) modular charging kiosks and quickly swap out the battery with one that’s freshly charged with renewable energy. Or, for more convenience, simply plug it in at home.
Want a new ride? Swap body styles.
Because Electric Cars have so few moving parts, the Aurica frame and drive system could easily last for 20 years or more with minimal maintenance. Instead of buying a new car every 2 to 5 years, you can just swap out an older body style for a brand new look for less than a third the price of a new car. Now that’s economical sustainability.
The Aurica E-Car Series will begin with four body styles all built to fit on the same standard chassis. You can get a sporty economy car, a mid-sized 4-door sedan, a stylish SUV hatchback, or a light pickup truck. More body styles and color combinations will be available every year. We will even assist custom body designers to offer more exotic designs that fit the chassis perfectly.
The best of everything.
The beauty of Aurica Motors electric car design is that you can make them with existing off-the-shelf car parts. This common supply base already exists. Someone just has to pull it all together. That’s what Aurica Motors is doing. We are sourcing and testing the best of the industry and adding our own innovations to create an electric car that does more for the people, the economy, and the environment than ever before.
Mar 10, 2010
AT&T Becomes Lead Customer for Ford Transit Connect Electric
Azure Dynamics Corporation today announced AT&T has agreed to purchase two of the first Ford Transit Connect Electric vans, the latest addition to AT&T's growing fleet of alternative-fuel vehicles.
The Ford Transit Connect Electric -- the all-electric version of the 2010 Ford Transit Connect, the North American Truck of the Year -- will be powered by Azure Dynamics' patented Force Drive(TM) electric drivetrain with an advanced lithium-ion battery from Johnson Controls-Saft. The vehicle, which goes on sale later this year, has a range of up to 80 miles on a single charge and will be rechargeable using either 240-volt or standard 120-volt outlets. It has a top speed of 75 miles per hour.
"Cleaner, alternative-fuel vehicles are the future of our corporate fleet, and the Transit Connect Electric represents a real breakthrough and will be a strong addition to our range of alternative-fuel vehicles," said Jerome Webber, vice president of fleet operations at AT&T. "It's exactly the kind of vehicle we envisioned when we mapped our long-term vision to invest up to $565 million to deploy more than 15,000 alternative-fuel vehicles through 2018." AT&T currently operates more than 77,000 vehicles in its corporate fleet, including 15 gasoline-powered Ford Transit Connect vehicles AT&T began piloting in 2009.
Scott T. Harrison, CEO of Azure Dynamics, said the Transit Connect Electric project is in line with his company's mission.
"Our business is built on great technology, committed partners and customers who want to improve efficiency while reducing their environmental footprint," Harrison said. "The Transit Connect Electric brings all of those elements together in a single package and is exactly on target with our goal at Azure of 'driving a world of difference.'"
According to Harrison, commercial vehicles are ideal candidates for electrification due to typical duty cycle characteristics like predictable drive routes and a return to a central location each night for recharging. The zero tailpipe emission Ford Transit Connect Electric also will help protect air quality in the urban environments where it operates.
By combining car-like driving dynamics with truck-like cargo capacity, Ford Transit Connect Electric is well-suited to the demands placed on urban delivery vehicles for small businesses and larger, corporate fleets.
The Transit Connect Electric is expected to offer lower cost of operation because recharging with electricity is generally less expensive than refueling with gasoline. Additionally, customers will benefit from lower maintenance costs as the electric drive train has far fewer moving parts to maintain.
"Ford Transit Connect was first introduced in the U.S. last year as a new fuel efficient alternative to larger commercial vehicles. Adding the electric option addresses a growing demand from our customers for sustainable vehicles for their fleets," said Gerry Koss, Ford fleet marketing manager. "This Transit Connect Electric represents the first in a family of electrified vehicles, including new hybrids, plug-in hybrids and all battery electric vehicles, which Ford will deliver over the next three years."
AT&T plans to take delivery of the Transit Connect Electric in late 2010.
About Azure Dynamics
Azure Dynamics Corporation (TSX: AZD & OTC: AZDDF) is a world leader in the development and production of hybrid electric and electric components and powertrain systems for commercial vehicles. Azure is strategically targeting the commercial delivery vehicle and shuttle bus markets and is currently working internationally with various partners and customers. The Company is committed to providing customers and partners with innovative, cost-efficient, and environmentally-friendly energy management solutions. For more information please visit www.azuredynamics.com.
About Ford Motor Company
Ford Motor Company, a global automotive industry leader based in Dearborn, Mich., manufactures or distributes automobiles across six continents. With about 198,000 employees and about 90 plants worldwide, the company's automotive brands include Ford, Lincoln, Mercury and Volvo. The company provides financial services through Ford Motor Credit Company. For more information regarding Ford's products, please visit www.ford.com.
About AT&T
AT&T Inc. (NYSE:T) is a premier communications holding company. Its subsidiaries and affiliates, AT&T operating companies, are the providers of AT&T services in the United States and around the world. Among their offerings are the world's most advanced IP-based business communications services, the nation's fastest 3G network and the best wireless coverage worldwide, and the nation's leading high speed Internet access and voice services. In domestic markets, AT&T is known for the directory publishing and advertising sales leadership of its Yellow Pages and YELLOWPAGES.COM organizations, and the AT&T brand is licensed to innovators in such fields as communications equipment. As part of their three-screen integration strategy, AT&T operating companies are expanding their TV entertainment offerings. In 2009, AT&T again ranked No. 1 in the telecommunications industry on FORTUNE®magazine's list of the World's Most Admired Companies. Additional information about AT&T Inc. and the products and services provided by AT&T subsidiaries and affiliates is available at http://www.att.com.
© 2010 AT&T Intellectual Property. All rights reserved. AT&T, the AT&T logo and all other marks contained herein are trademarks of AT&T Intellectual Property and/or AT&T affiliated companies. All other marks contained herein are the property of their respective owners.
The Ford Transit Connect Electric -- the all-electric version of the 2010 Ford Transit Connect, the North American Truck of the Year -- will be powered by Azure Dynamics' patented Force Drive(TM) electric drivetrain with an advanced lithium-ion battery from Johnson Controls-Saft. The vehicle, which goes on sale later this year, has a range of up to 80 miles on a single charge and will be rechargeable using either 240-volt or standard 120-volt outlets. It has a top speed of 75 miles per hour.
"Cleaner, alternative-fuel vehicles are the future of our corporate fleet, and the Transit Connect Electric represents a real breakthrough and will be a strong addition to our range of alternative-fuel vehicles," said Jerome Webber, vice president of fleet operations at AT&T. "It's exactly the kind of vehicle we envisioned when we mapped our long-term vision to invest up to $565 million to deploy more than 15,000 alternative-fuel vehicles through 2018." AT&T currently operates more than 77,000 vehicles in its corporate fleet, including 15 gasoline-powered Ford Transit Connect vehicles AT&T began piloting in 2009.
Scott T. Harrison, CEO of Azure Dynamics, said the Transit Connect Electric project is in line with his company's mission.
"Our business is built on great technology, committed partners and customers who want to improve efficiency while reducing their environmental footprint," Harrison said. "The Transit Connect Electric brings all of those elements together in a single package and is exactly on target with our goal at Azure of 'driving a world of difference.'"
According to Harrison, commercial vehicles are ideal candidates for electrification due to typical duty cycle characteristics like predictable drive routes and a return to a central location each night for recharging. The zero tailpipe emission Ford Transit Connect Electric also will help protect air quality in the urban environments where it operates.
By combining car-like driving dynamics with truck-like cargo capacity, Ford Transit Connect Electric is well-suited to the demands placed on urban delivery vehicles for small businesses and larger, corporate fleets.
The Transit Connect Electric is expected to offer lower cost of operation because recharging with electricity is generally less expensive than refueling with gasoline. Additionally, customers will benefit from lower maintenance costs as the electric drive train has far fewer moving parts to maintain.
"Ford Transit Connect was first introduced in the U.S. last year as a new fuel efficient alternative to larger commercial vehicles. Adding the electric option addresses a growing demand from our customers for sustainable vehicles for their fleets," said Gerry Koss, Ford fleet marketing manager. "This Transit Connect Electric represents the first in a family of electrified vehicles, including new hybrids, plug-in hybrids and all battery electric vehicles, which Ford will deliver over the next three years."
AT&T plans to take delivery of the Transit Connect Electric in late 2010.
About Azure Dynamics
Azure Dynamics Corporation (TSX: AZD & OTC: AZDDF) is a world leader in the development and production of hybrid electric and electric components and powertrain systems for commercial vehicles. Azure is strategically targeting the commercial delivery vehicle and shuttle bus markets and is currently working internationally with various partners and customers. The Company is committed to providing customers and partners with innovative, cost-efficient, and environmentally-friendly energy management solutions. For more information please visit www.azuredynamics.com.
About Ford Motor Company
Ford Motor Company, a global automotive industry leader based in Dearborn, Mich., manufactures or distributes automobiles across six continents. With about 198,000 employees and about 90 plants worldwide, the company's automotive brands include Ford, Lincoln, Mercury and Volvo. The company provides financial services through Ford Motor Credit Company. For more information regarding Ford's products, please visit www.ford.com.
About AT&T
AT&T Inc. (NYSE:T) is a premier communications holding company. Its subsidiaries and affiliates, AT&T operating companies, are the providers of AT&T services in the United States and around the world. Among their offerings are the world's most advanced IP-based business communications services, the nation's fastest 3G network and the best wireless coverage worldwide, and the nation's leading high speed Internet access and voice services. In domestic markets, AT&T is known for the directory publishing and advertising sales leadership of its Yellow Pages and YELLOWPAGES.COM organizations, and the AT&T brand is licensed to innovators in such fields as communications equipment. As part of their three-screen integration strategy, AT&T operating companies are expanding their TV entertainment offerings. In 2009, AT&T again ranked No. 1 in the telecommunications industry on FORTUNE®magazine's list of the World's Most Admired Companies. Additional information about AT&T Inc. and the products and services provided by AT&T subsidiaries and affiliates is available at http://www.att.com.
© 2010 AT&T Intellectual Property. All rights reserved. AT&T, the AT&T logo and all other marks contained herein are trademarks of AT&T Intellectual Property and/or AT&T affiliated companies. All other marks contained herein are the property of their respective owners.
Ballard to Receive DOE Funding to Advance Non-Automotive Fuel Cell Commercialization
Ballard Power Systems announced today that it has $6.2 million in project funding from the U.S. Department of Energy (DOE) under contract over a four year period. Ballard Material Products, a U.S. subsidiary of Ballard Power Systems, was awarded $4.1 million as prime for a contract that will focus on improvements in fuel cell durability and cost. Additionally, Ballard will be sub-contractor to leading U.S. technology organizations for several other fuel cell research and development projects funded by the DOE.
"We are excited to be working with a technology leader such as Ballard Power Systems," said Dr. Rod Borup, Fuel Cell Program Manager, Institute for Hydrogen and Fuel Cell Research at Los Alamos National Laboratory, one of Ballard's project partners. "This is important work in support of the DOE goal to move fuel cell technology closer to large scale commercialization. Our collaborations with Ballard are in the areas of understanding and improving fuel cell durability and reducing technology cost, which are the primary enablers to rapid market adoption of fuel cell systems."
Over eighty percent of the announced DOE funding has been allocated to projects aimed at increased durability and cost reduction, with the remaining funds focused on water management modeling. The project for which Ballard Material Products will be prime is meant to improve the understanding of fuel cell materials and components degradation, leading to recommended mitigation strategies to facilitate further commercialization. Resulting advancements will facilitate commercialization of fuel cells for a range of applications, including stationary power generation.
In addition to Los Alamos National Laboratory, Ballard will be partnering with other leading U.S. technology organizations, including Lawrence Berkeley National Laboratory, Sandia National Laboratory, Georgia Institute of Technology, Michigan Technical University, University of Hawaii at Manoa and University of New Mexico.
"The receipt of significant funding from the DOE clearly demonstrates the Department of Energy's interest in fuel cell market adoption," said Dr. Christopher Guzy, Chief Technology Officer at Ballard Power Systems. "This funding is completely aligned with Ballard's plans to continue investing in strategic enhancements of non-automotive fuel cell products."
About Ballard Power Systems
Ballard Power Systems (TSX: BLD; NASDAQ: BLDP) provides clean energy fuel cell products enabling optimized power systems for a range of applications. To learn more about Ballard, please visit www.ballard.com.
"We are excited to be working with a technology leader such as Ballard Power Systems," said Dr. Rod Borup, Fuel Cell Program Manager, Institute for Hydrogen and Fuel Cell Research at Los Alamos National Laboratory, one of Ballard's project partners. "This is important work in support of the DOE goal to move fuel cell technology closer to large scale commercialization. Our collaborations with Ballard are in the areas of understanding and improving fuel cell durability and reducing technology cost, which are the primary enablers to rapid market adoption of fuel cell systems."
Over eighty percent of the announced DOE funding has been allocated to projects aimed at increased durability and cost reduction, with the remaining funds focused on water management modeling. The project for which Ballard Material Products will be prime is meant to improve the understanding of fuel cell materials and components degradation, leading to recommended mitigation strategies to facilitate further commercialization. Resulting advancements will facilitate commercialization of fuel cells for a range of applications, including stationary power generation.
In addition to Los Alamos National Laboratory, Ballard will be partnering with other leading U.S. technology organizations, including Lawrence Berkeley National Laboratory, Sandia National Laboratory, Georgia Institute of Technology, Michigan Technical University, University of Hawaii at Manoa and University of New Mexico.
"The receipt of significant funding from the DOE clearly demonstrates the Department of Energy's interest in fuel cell market adoption," said Dr. Christopher Guzy, Chief Technology Officer at Ballard Power Systems. "This funding is completely aligned with Ballard's plans to continue investing in strategic enhancements of non-automotive fuel cell products."
About Ballard Power Systems
Ballard Power Systems (TSX: BLD; NASDAQ: BLDP) provides clean energy fuel cell products enabling optimized power systems for a range of applications. To learn more about Ballard, please visit www.ballard.com.
Mar 5, 2010
Today, LUMENEO presents the serial model of the SMERA
The SMERA is now ready to commute into the urban and out-of-town traffic. Originally designed to shift and park with ease, the SMERA has a dreaming size: 86 cm width and 2,50 m length.
Do not suffer traffic jam or bad weather, park easily and safely drive.
The SMERA opens a new way of mobility. LUMENEO is currently working on the M1 European homologation for the SMERA. This car homologation is the first one for such innovative vehicle, final certificate will allow to drive on all European roads.
After several exhibitions where the SMERA has been presented, we have collected visitors' suggestions. This final version offers to the driver and his passenger more inside roominess.
For this first year of production, Lumeneo plans a progressive start. In 2011, rhythm will increase to match the French and European demands.
Entirely electric, a car driving licence is compulsory to drive the SMERA.
The alliance of aestheticism ...
A VERY URBAN LINE
Purity and delicacy of lines have guided the hand of the SMERA designers. With its only 86 cm of width and 2.50 m of length, the SMERA has an exclusive size to slip into the traffic and park without constraint. Its very fluid lines are emphasized by its automatic tilt in curves.
Getting onboard is easy, thanks to two large lateral doors. It allows getting in by the right or the left side, up to the place of parking. The SMERA has an aluminium protective 3D frame and a closed body. Seat belts and crash box complete the passive safety.
Five colours are available, but the choice of a specific colour is always possible.
A PREMIUM ONBOARD
Inside, the visibility is maximal with a wide glass surface which provides a panoramic view on traffic. The driver is comfortably held in his leather seat, protected by his seatbelt, without helmet. His seat can be fold away to let the passenger get in the back seat. Cockpit includes a LCD screen which displays all intuitive commands. The SMERA has a trunk which can easily receive daily bags (attaché-case, shopping bags...).
...and technology.
One special features of the SMERA is its automatic tilting system, to fit the curves with a new sensation. The driver is taking care of nothing, the intuitive handling provides a real driving comfort.
In the heart of the SMERA, an electronic system manages all the parameters of the vehicle, starting from the signals provided by an integrated inertial system. According to the dynamic parameters of the car, the turning curves, the selected driving mode and the road quality, it determines the optimal tilting angle. It is a servomotor controlled by the calculator which fulfils the function automatically by moving the cabin and the four wheels.
ECOLOGICAL BY NATURE
Electric since its design, the SMERA is particularly ecological. Its operation generates no local pollution, no noise and no smoke. Its maintenance is minimal because electric motor have a very long life and its recycling is simple.
The SMERA is equipped with two electric brushless motors with permanent magnets for its propulsion, especially designed for this purpose. These motors offer a 1,000 Nm torque at the rear wheels from the start unlike thermal engines, where the maximum torque is only available at high speed.
Each motor weighs less than 30 Kg and is made up 98 % of pure metals, aluminium, copper and irons o its recycling is simple. It also avoids all the pollution created by a thermal engine: oils, catalytic exhausts, heavy metals.
The motors have been developed to answer precisely to the needs of the SMERA and to optimise the weight/power ratio. At Eeach braking action, the motors are transformed into an alternator to convert kinetic energy into electricity injected in the batteries, increasing the autonomy of the SMERA.
Brushless motors offer the main advantage to have no friction parts that makes it possible to have no maintenance and an excellent lifetime, nearly 200 000 km.
ELECTRICTY, ENERGY OF THE FUTURE
The energy source of the SMERA is a pack of batteries offering a 133 V tension and a 10 kWh capacity. Made of Lithium technology, these up-to-date elements meet all the needs of the SMERA. Thanks to its integrated charger and a 3 meters cable, the SMERA can be reloaded in all domestic plugs (230 V, 16 A).
The global awareness of the electric revolution will cause the multiplication of the charging plugs inside buldings, parkings and streets.
You just have to get a new reflex : plug it in the night and unplug it in the always have a 150 km maximum autonomy.
For this, the SMERA asks only for a 0,7 euro/100Km refill (standard cost French electricity). This means a 6 000 € saving for 100.000 km versus a thermal motorisation (of average consumption 5 l /100km).
The SMERA Lithium batteries are designed to operate at least 8 years, even if used every day.
AN ELECTRONIC COMING FROM AEROSPACE
From motors to wheels, a direct belt transmission is installed. The electric motors display a maximal torque when starting and deliver their power in such manner that it is not necessary to couple them with a gearbox.
The SMERA has two motor controllers and a central UC. They always work and the central UC supervises the controllers via a CAN bus, checking all results and calculation. In case of problem, the
central UC is acting as arbitrator, by adjusting the data. This architecture, already approved in aerospace, allows having a high reliability system. The electronic manages each millisecond the rates and the couples of the motors, so the SMERA can easily operate.
Do not suffer traffic jam or bad weather, park easily and safely drive.
The SMERA opens a new way of mobility. LUMENEO is currently working on the M1 European homologation for the SMERA. This car homologation is the first one for such innovative vehicle, final certificate will allow to drive on all European roads.
After several exhibitions where the SMERA has been presented, we have collected visitors' suggestions. This final version offers to the driver and his passenger more inside roominess.
For this first year of production, Lumeneo plans a progressive start. In 2011, rhythm will increase to match the French and European demands.
Entirely electric, a car driving licence is compulsory to drive the SMERA.
The alliance of aestheticism ...
A VERY URBAN LINE
Purity and delicacy of lines have guided the hand of the SMERA designers. With its only 86 cm of width and 2.50 m of length, the SMERA has an exclusive size to slip into the traffic and park without constraint. Its very fluid lines are emphasized by its automatic tilt in curves.
Getting onboard is easy, thanks to two large lateral doors. It allows getting in by the right or the left side, up to the place of parking. The SMERA has an aluminium protective 3D frame and a closed body. Seat belts and crash box complete the passive safety.
Five colours are available, but the choice of a specific colour is always possible.
A PREMIUM ONBOARD
Inside, the visibility is maximal with a wide glass surface which provides a panoramic view on traffic. The driver is comfortably held in his leather seat, protected by his seatbelt, without helmet. His seat can be fold away to let the passenger get in the back seat. Cockpit includes a LCD screen which displays all intuitive commands. The SMERA has a trunk which can easily receive daily bags (attaché-case, shopping bags...).
...and technology.
One special features of the SMERA is its automatic tilting system, to fit the curves with a new sensation. The driver is taking care of nothing, the intuitive handling provides a real driving comfort.
In the heart of the SMERA, an electronic system manages all the parameters of the vehicle, starting from the signals provided by an integrated inertial system. According to the dynamic parameters of the car, the turning curves, the selected driving mode and the road quality, it determines the optimal tilting angle. It is a servomotor controlled by the calculator which fulfils the function automatically by moving the cabin and the four wheels.
ECOLOGICAL BY NATURE
Electric since its design, the SMERA is particularly ecological. Its operation generates no local pollution, no noise and no smoke. Its maintenance is minimal because electric motor have a very long life and its recycling is simple.
The SMERA is equipped with two electric brushless motors with permanent magnets for its propulsion, especially designed for this purpose. These motors offer a 1,000 Nm torque at the rear wheels from the start unlike thermal engines, where the maximum torque is only available at high speed.
Each motor weighs less than 30 Kg and is made up 98 % of pure metals, aluminium, copper and irons o its recycling is simple. It also avoids all the pollution created by a thermal engine: oils, catalytic exhausts, heavy metals.
The motors have been developed to answer precisely to the needs of the SMERA and to optimise the weight/power ratio. At Eeach braking action, the motors are transformed into an alternator to convert kinetic energy into electricity injected in the batteries, increasing the autonomy of the SMERA.
Brushless motors offer the main advantage to have no friction parts that makes it possible to have no maintenance and an excellent lifetime, nearly 200 000 km.
ELECTRICTY, ENERGY OF THE FUTURE
The energy source of the SMERA is a pack of batteries offering a 133 V tension and a 10 kWh capacity. Made of Lithium technology, these up-to-date elements meet all the needs of the SMERA. Thanks to its integrated charger and a 3 meters cable, the SMERA can be reloaded in all domestic plugs (230 V, 16 A).
The global awareness of the electric revolution will cause the multiplication of the charging plugs inside buldings, parkings and streets.
You just have to get a new reflex : plug it in the night and unplug it in the always have a 150 km maximum autonomy.
For this, the SMERA asks only for a 0,7 euro/100Km refill (standard cost French electricity). This means a 6 000 € saving for 100.000 km versus a thermal motorisation (of average consumption 5 l /100km).
The SMERA Lithium batteries are designed to operate at least 8 years, even if used every day.
AN ELECTRONIC COMING FROM AEROSPACE
From motors to wheels, a direct belt transmission is installed. The electric motors display a maximal torque when starting and deliver their power in such manner that it is not necessary to couple them with a gearbox.
The SMERA has two motor controllers and a central UC. They always work and the central UC supervises the controllers via a CAN bus, checking all results and calculation. In case of problem, the
central UC is acting as arbitrator, by adjusting the data. This architecture, already approved in aerospace, allows having a high reliability system. The electronic manages each millisecond the rates and the couples of the motors, so the SMERA can easily operate.
Subscribe to:
Posts (Atom)